2024/04/22
『機械設備のメンテナンス』
Maintenance of mechanical equipment
1. 設備・機械のメンテナンス・保守・保全の違い
製造業でよく耳にする、メンテナンス・保守・保全という言葉。実は、メンテナンスと保守は同じ意味合いの用語ですが、保全はプロセスで異なる部分がある。定期的に機械や設備の稼働状況を確認したり、故障しそうにないか調査したりする作業が、メンテナンス・保守。一方、保全には3つのプロセスがあり、メンテナンスや保守と比べイメージしにくい部分である。
ここでは、メンテナンス・保守・保全の意味とそれぞれの違いを掘り下げて解説する。
1.1 保守とメンテナンスの違い
保守とは、設備や機械が正常に動作するよう、点検・整備することを指します。一方のメンテナンスは、システムやネットワークなどの保守・点検作業を意味する用語である。いずれも、機械や生産設備の点検や修理を意味しており、製造業の現場では同じ意味合いで使用されるケースが多く見られる。
したがって、保守とメンテナンスを区別する必要はなく、「保守=メンテナンス」と考えて良い。
1.2 保守・メンテナンスと保全の違い
保守・メンテナンスと類似した用語に、保全があげられる。保全とは、設備・機械の点検をおこない、安全性を保つことを指す。
保守・メンテナンスと同義にも思いますが、保全は「機器や生産設備が壊れないようにする」というニュアンスが強い点が特徴でる。
一方のメンテナンス・保守には「機械や生産設備が故障したら修理する」という意味合いも含まれる。
保守・メンテナンスと保全の違いをまとめると、以下のようになる。
・保守・メンテナンス:設備・機械が正常に動作するよう点検・修理すること
・保全:設備・機械の異常を回避するため、維持管理すること
ただし、メンテナンス・保守・保全の定義は人(会社)によっても解釈が異なるため、注意が必要である。
2. 設備・機械保全の種類
設備・機械の保全は、大きく以下の3種類に分類される。ここででは、上記3種類の保全をさらに細分化し、それぞれの違いを解説する。
・事後保全
・予防保全
・予知保全
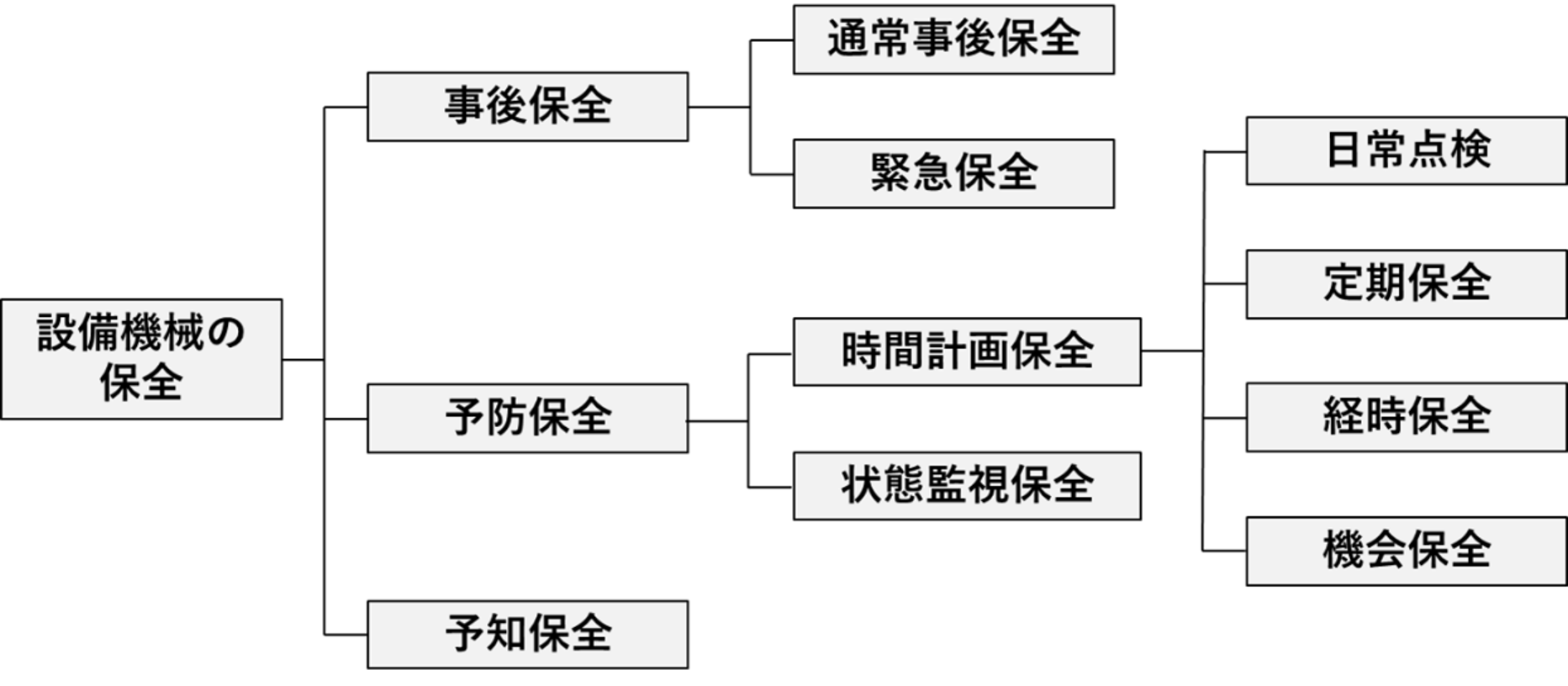
図1. 設備・機械保全の分類
2.1 設備・機械保全:事後保全
事後保全とは、設備や機械が故障・停止した場合に、原因を調査し対処することである。主に、機能低下型故障と機能停止型故障の2つを対象としており、それぞれ以下の違いがある。
・機能低下型故障:設備・機械の性能が低下する故障のこと
・機能停止型故障:設備・機械が停止する故障のこと
また、事前の予防保全によって部品交換・修理された設備・機械が故障した場合は、緊急保全で対処する。
一方、予防保全の対象に該当しない設備・機械が故障した場合は、通常事後保全。呼び名こそ違いうが、設備・機械の呼称がトリガーとなって実施される点では同義である。
また、設備・機械の故障は生産工程の遅延や停止にもつながるため、早急な対処が求められる。
2.2 設備・機械保全:予防保全
予防保全とは、保全計画をもとに設備や機械を定期的に点検・修理、部品交換することである。設備・機械が壊れたり、異常をきたしたりする前に、対処するのが目的である。
さらに、予防保全は以下2種類に分類される。
・時間基準保全:部品の状態に関係なく、一定の期間内に使用した部品を交換
・状態基準保全:部品の状態を確認し、劣化状況によって部品を交換
時間基準保全と状態基準保全は、ともに設備・機械の故障を未然に防ぐためのものであるが、保全するタイミングが異なってくる。
2.2.1 時間計画保全
時間計画保全とは、TBM(Time Based Preventive Maintenance)とも呼ばれ、一定の時間間隔で実施される保全のことである。設備・機械の交換すべき部品をリストアップし、過去のデータをもとに適正な交換期間を割り出す。時間計画保全では、たとえ故障や異常が見られない場合でも部品を交換するため、保全コストが大きくなりがちである。
ただし、部品交換計画どおりに実施するため、部品在庫を最小限に抑えられる点がメリットになる。
2.2.2 状態監視保全
状態監視保全は、CBM(Condition Based Maintenance)とも呼ばれる保全方法。設備・機械の状態を点検し、異常が見られた場合にその状態に合わせて部品を交換・修理する方法である。時間計画保全と異なり、必要な部分のみの交換で済むため、保全コストを抑えやすい点が特徴である。
一方、点検回数が多いと手間がかかるうえに、部品在庫を常時抱えておく必要がある点はデメリットといえる。
2.3 設備・機械保全:予知保全(予兆保全)
予知保全は、設備や機会故障の予兆を見極め、事前に対処する保全方法である。予知保全は状態監視保全に近い考え方であるが、IoTやAIなどのデジタル技術を活用し継続的にデータを収集・分析する点が特徴である。デジタル技術の発展やDX推進の影響を受け、近年注目を集めている保全方法である。
すでに一部の製造業企業では、設備・機械にIoTセンサーを取り付け、故障の予兆をAIで分析している事例も多く見られるようになった。
3. 設備や機械メンテナンス・保守の必要性
設備や機械をメンテナンス・保全する目的は、主に以下の4つである。
・機器・設備の耐用年数を延ばす
・故障を最小限に抑える
・稼働率を上げる
・物損の発生を防ぐ
メンテナンス・保全は、工場の設備や機械が安定して稼働し、製品の品質を確保するために欠かせない。さらに、設備の老朽化による事故を防ぐ役割もある。
メンテナンス・保全を実施する目的は次ようになる。
3.1 メンテナンスの必要性1:設備や機械の耐用年数を延ばす
設備や機械の定期的なメンテナンスによって、締結しているボトルやナットの締め込み作業や給油、周辺部品や付帯設備が傷つくのを防ぐことで、耐久性を上げ耐用年数を延ばしている。工場の生産設備には数多くの部品があり、使用するほど劣化するため、いずれは故障することになる。部品が故障すると、性能の低下や生産設備が停止する恐れがあるため、定期的なメンテナンスは欠かせない。
とはいえ、無駄な部品交換が多いと、コストが膨らみ、生産物の価格が上がってしまう。コスト増加を防ぐためには、生産設備にある部品の耐用年数を延ばすメンテナンスや保全が必要になる。
3.2 メンテナンスの必要性2:故障を最小限に抑える
工場の設備や機械が故障すると、不良品の発生や生産計画の遅れにつながる。故障状況が悪いと、生産ラインを止める場合もあり、製品不良分を生産する材料費や光熱費、従業員の残業にかかる人件費など、生産コストが増加してしまう。故障による生産コストの増加を防ぐには、予防保全が有効である。
さらに、故障した設備や機械を修理するだけでなく、事後保全を実施すれば再発防止も期待できる。
3.3 メンテナンスの必要性3:稼働率を上げる
設備や機械の稼働率が上がれば、運用や保守にかかるコストの大幅な削減が可能である。故障を未然に防ぐことで、製造が止まる状態を回避できるため、工場の生産性が向上する。
3.4 メンテナンスの必要性4:物損の発生を防ぐ
工場の生産設備では、常に何らかの製造を行っている。しかし、生産設備の性能が低下したことに気づかず生産が進むと、不良品が大量に発生し、大きな損失につながる恐れがある。不良品となった製造物の破棄は、お金をドブに捨てる行為と同じといえる。このような物損(不良品)の発生を防ぐのも、メンテナンスや保全の目的である。
4. 設備や機械をメンテナンス・保全する際のポイント3つ
設備や機械のメンテナンスや保全において、おさえるべきポイントは以下の3つである。
・速さ
・改善後の行動
・新しい技術の取り入れ
故障や不具合を素早く見つけ改善するだけでなく、機能を向上させることが重要である。
それでは、設備や機械をメンテナンス・保全する際のポイントを以下に示す。
4.1 ポイント1:速さ
定期的なメンテナンスや保全で重要となるのが、対応の速さである。中でも事後保全は、異常や故障を見つけてから部品を交換する。交換中は設備や機械を停止する必要があるため、原因を即座に特定し再稼働を目指さなければならない。
原因の究明や修理に時間がかかるほど、工場の生産性や機能性は低下してしまう。素早く適切に判断するためにも、設備・機械に関する知識やノウハウを現場従業員へ共有することが大切になる。
4.2 ポイント2:改善後の行動
故障を見つけ修理した後、再びトラブルが発生しないように改善したり、メンテナンス効率を向上させたりすることも重要である。メンテナンスでは故障箇所の修理だけで終わる場合も多いが、今後「より良くするにはどうすればよいのか」を考えることも大切である。
事後保全に関しては、改善と向上がセットとなる。故障した際の代替機の用意や、修理会社への連絡手段を確認するなど、次回以降のトラブルに向けた対策を取ることも重要である。
4.3 ポイント3.新しい技術の取り入れ
予防保全や予知保全では、設備を新しくする際に新しい技術や工夫を取り入れることがポイントである。従来と同じ設備を導入するよりも、新しい技術や工夫を取り入れた方がコストを抑えられる場合がある。
工場の設備や機械を改良すれば、操作性や耐久性、安全性が上がるだけでなく、メンテナンスや修理にかかるコストを削減でき、部品劣化の防止も可能である。
5. 機械メンテナンス・保守業務のデジタル化・DX推進
かつての製造業では、設備や機械が故障する前に対処する、事前保全が重要とされていた。しかし、AIやIoTなどのデジタル技術やERPシステムなどのITテクノロジーが登場したことで、状況は一変している。
設備や機械が故障する予兆を見つけ、迅速に対処する予知保全が注目されている。デジタル技術やITテクノロジーを活用すると、人が多くの手を加えずとも、設備・機械の様々なデータをリアルタイムで取得でき、クラウド上のデータベースで管理・分析することができるようになった(図2. 予兆診断システムの事例)。
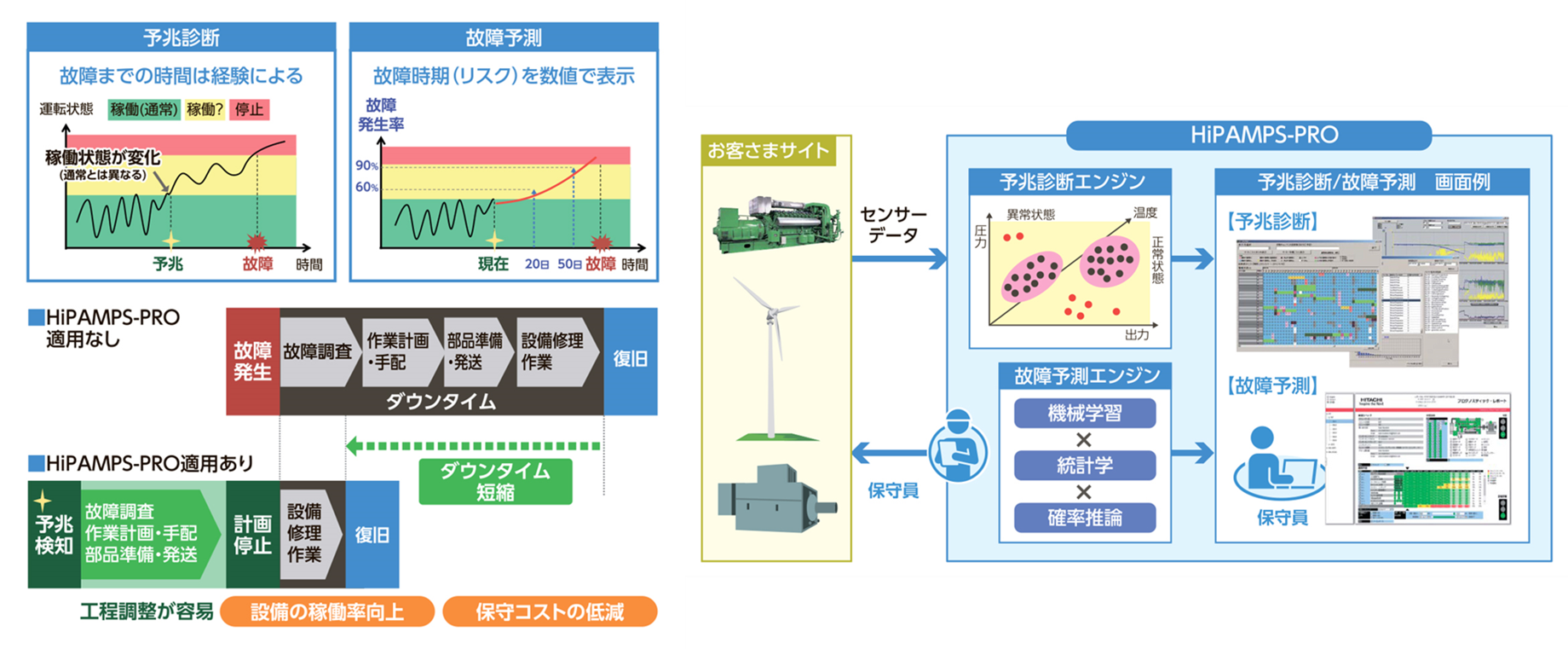
図2. 事例「予兆診断システム(HIPAMPS)」出所:日立パワーソリューションズ(株)
また人では気がつかない予兆を早期に発見・対処でき、工場の稼働率向上が期待できる。
こうした予知保全の実現に欠かせないのが、ERP(Enterprise Resource Planning)システムである。ERPシステムは、あらゆるシステムやデジタルテクノロジーと連携し、膨大な量のデータを一元管理・分析できるシステムである。いわば予知保全の中核を担うシステムとなるため、メンテナンス・保全業務のDX化に向けて積極的に導入が進むと考えられる。
6. 機械メンテナンス・保守、保全の今後の展開
本レポートでは、製造業に欠かせないメンテナンス・保守・保全の違いを概要について解説した。メンテナンスと保守は同じ意味合いの用語であり、保全は以下の違いがあることを述べた。
・保守・メンテナンス:設備・機械が正常に動作するよう点検・修理すること
・保全:設備・機械の異常を回避するため、維持管理すること
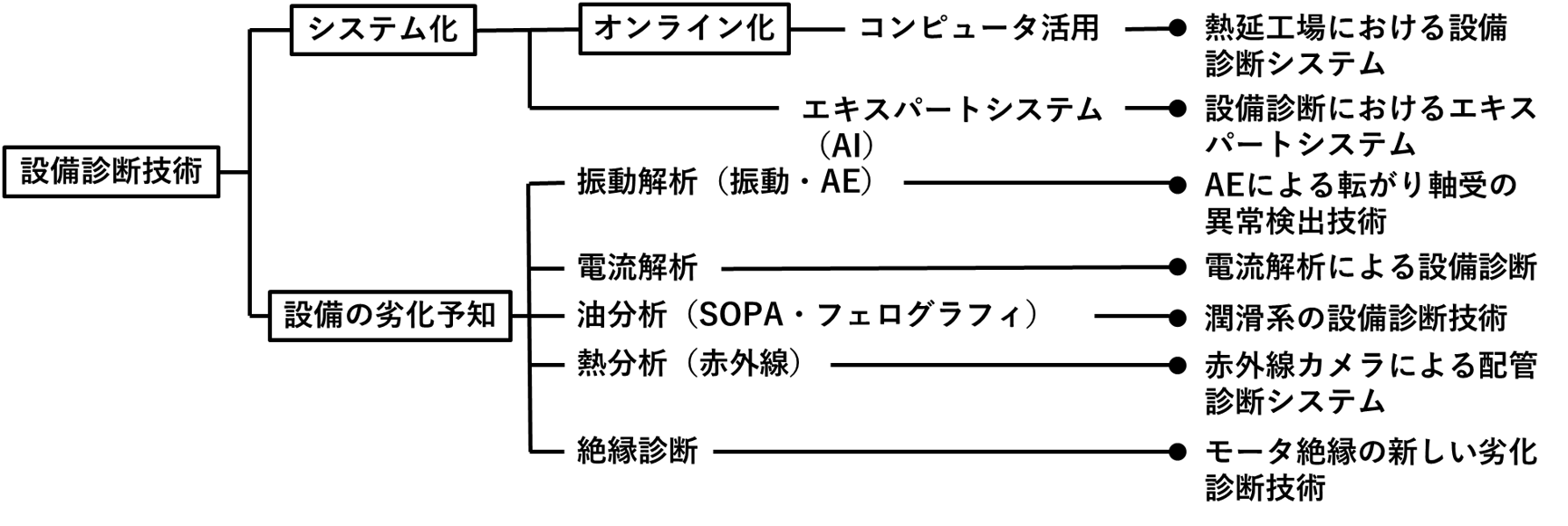
図3. 設備診断技術の例
近年、デジタル化やDX推進の影響を受け、故障する予兆をデジタル技術(図3. 設備診断技術の例)で発見し、迅速に対処する予知保全が注目されていることから、ERPシステムが今後の中核となって進められると考えられる。
以上
【参考引用先】
1. 「工場のメンテナンスは何をする?基礎知識やコストを徹底解説」(株)FAプロダクツ
HP お役立ち情報:https://jss1.jp/column/column_145/
2. 「工場の生産設備メンテナンス解説!トラブル・改善事例も紹介」(株)FAプロダクツ
HP お役立ち情報:https://jss1.jp/column/column_149/
3. 「予兆診断システム(HIPAMPS)」日立パワーソリューションズ(株)HP:
https://www.hitachi-power-solutions.com/
4. 機械設計 連載『搬送装置のロボット化で進める自動化生産ラインの構築術
最終回:「搬送装置の保全とチョコ停防止対策」』2023年12月号 P98 – P105