2024/05/07
『機械設備のリスクアセスメント』
Risk assessment of machinery and equipment
1.リスクアセスメントの目的と実施手順
【1】リスクアセスメントとは
リスクアセスメントとは、作業場における危険性又は有害性を特定し、それによる発生のおそれのある災害(健康障害を含む)の重篤度(災害の程度)とその災害が発生する可能性の度合を組み合わせてリスクを見積り、そのリスクの大きさに基づいて対策の優先度を決めた上で、リスクの除去又は低減の措置を検討し、その結果を記録する一連の手法である。リスクアセスメントによって検討された措置は、安全衛生計画に盛り込み、計画的に実施する必要がある。その手順は概ね図1. のようになる。

図1. リスクアセスメントの実施手順
【2】リスクアセスメントの目的と効果
1)リスクアセスメントの目的
リスクアセスメントを導入し実施する、主な目的は次に示す通りである。
【目的】
職場のみんなが参加して、職場にある危険の芽(リスク)とそれに対する対策の実情を知って、災害に至るおそれのあるリスクを事前にできるだけ取り除いて、労働災害が生じないような快適な職場にする。
2)リスクアセスメントの効果
リスクアセスメントを実施することにより、次のような効果が期待できる。
【効果】
①職場のリスクが明確になる
②職場のリスクに対する認識を、管理者を含め職場全体で共有できる
③安全対策について、合理的な方法で優先順位を決めることができる
④残されたリスクについて「守るべき決め事」の理由が明確になる
⑤職場全員が参加することにより「安全」に対する感受性が高まる
など、期待できる。
3)リスクアセスメントの法的位置付け
【位置付け】
労働安全衛生法第28条の2により、各業種では、リスクアセスメントの実施に努めなければならない。
【3】リスクアセスメントの実施手順
リスクアセスメントは、危険性又は有害性の特定からスタートする。作業場に存在する危険性又は有害性をいかに特定するかが、リスクアセスメントを効果的なものにするか否かにかかっている。
1)労働災害(健康障害を含む)が発生する仕組み
労働災害は、危険性又は有害性と人(作業者)の両者の存在があって、発生する。どちらかが存在するだけでは、労働災害には至らない。例えばただ単に刃物があるだけでは、災害にならず、それを人が持って(使用して)初めて災害にいたるリスクが発生する。この状態で、安全衛生対策の不備、不具合等があった場合、労働災害となる。これを図2. に示す。

図2. 危険性又は有害性から労働災害(健康障害を含む)に至るプロセス
2)リスクアセスメント導入の実施手順
リスクアセスメントを実施する場合の実施手順は、次の図3. の通りである。
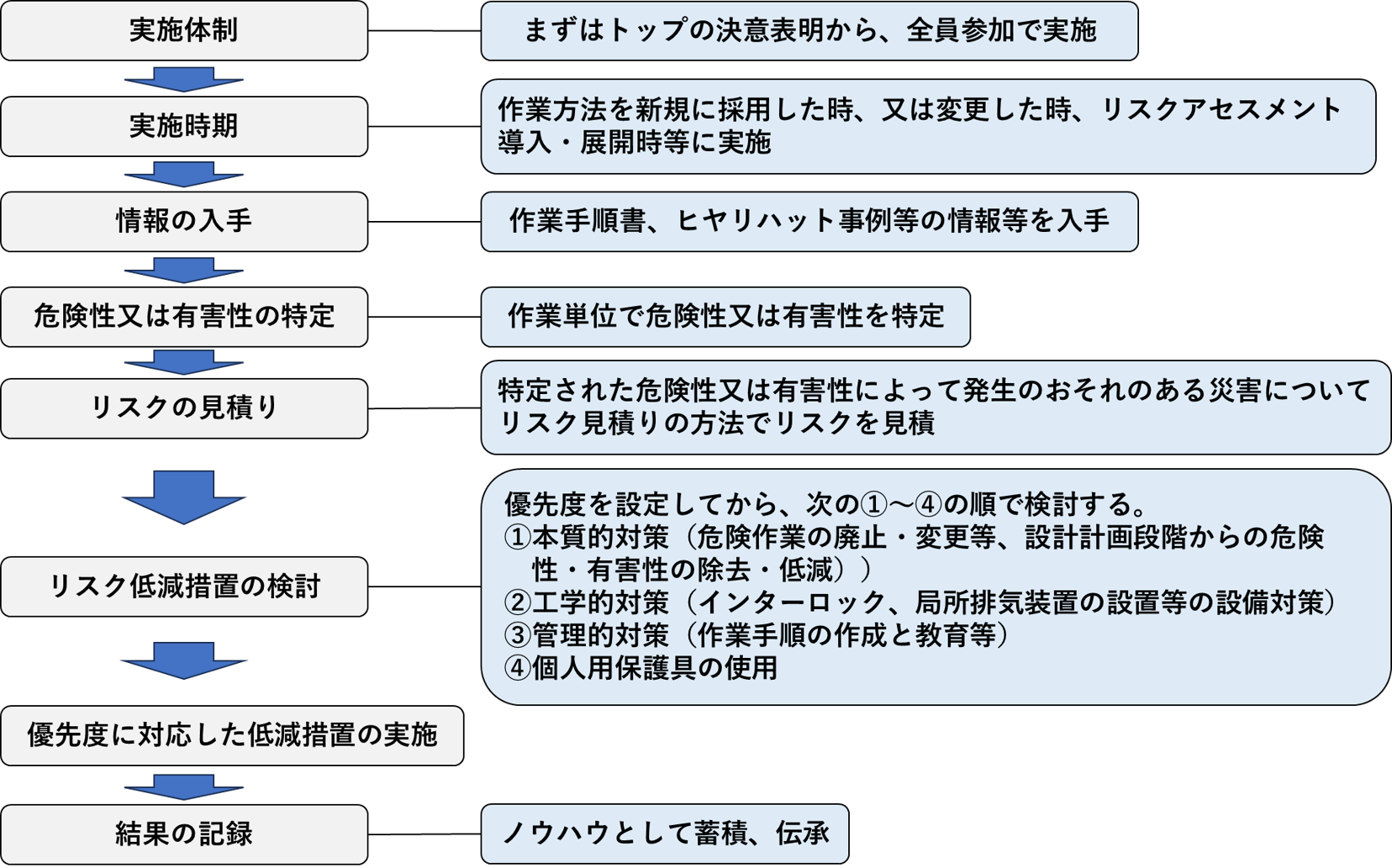
図3. リスクアセスメント導入の実施手順
実施する場合、企業全体が一斉に展開できればよいが、特定の部門、特定の事業所、店舗等から実施し、その結果に基づいて順次他の部門、事業所、店舗等に拡げて行くことも有効な方法である。ともかくリスクアセスメントの手法で「先ずはやってみる」という姿勢で取り組むことが大切である。
3)実施体制について(経営トップの決意表明と推進組織)
・リスクアセスメントを導入する場合、経営のトップは、従業員や関係者に自らの意思として「リスクアセスメントを行う」ことを宣言する必要がある
・事業所や店舗のトップ(総括安全衛生管理者)が実施を統括管理する
・事業場や店舗の安全管理者、衛生管理者等が実施を管理する
・安全衛生委員会等を活用し、労働者を参画させる
・その職場の作業指揮者(職長)を参画させる
・必要な教育を実施しする
などにより実施体制とする(図4. 参照)。
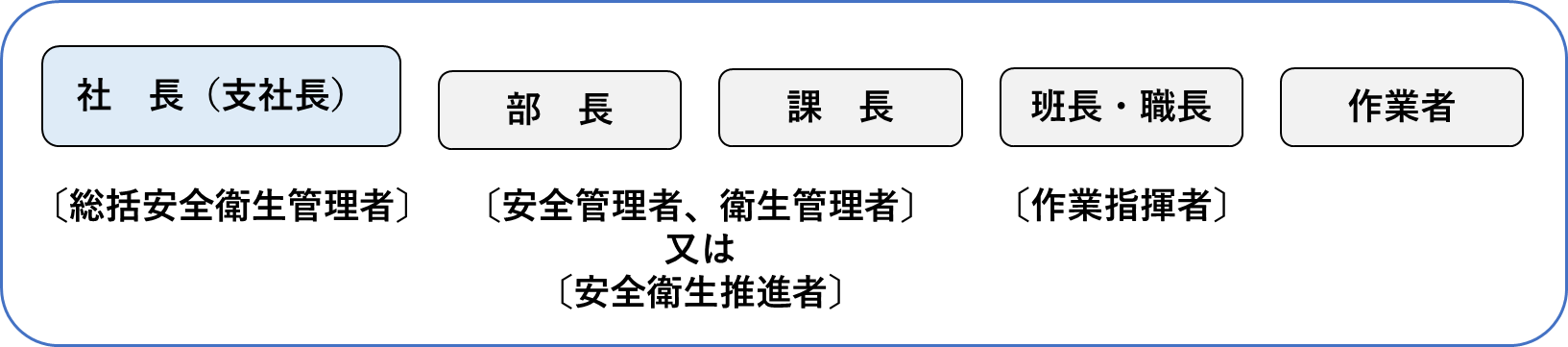
図4. 推進体制の例
4)実施時期
実施時期については、設備又は作業方法を変更したり、新規に採用した場合や、労働災害が発生した場合等があるが、「先ずは、リスクアセスメントをやってみよう」ということで、危ないと思われる作業・作業場所を導入時の対象として絞り込み、できるところからリスクアセスメントを始めて行くことが大切である。
5)情報の入手
入手すべき情報としては、ヒヤリハット(労働災害を伴わない危険な事象)、KYK(危険予知活動)の事例、安全パトロール結果、類似災害情報等があり、これらを作業者から報告させる仕組みが必要になる。
(注)「ヒヤリハット」とは、労働災害には至らないが、人が危険な状況や環境条件等に感覚的に「あぶない」、「有害だ」と感じ、ヒヤリとしたり、ハットした出来事を表す言葉である。これをメモ帳やノートに書留めておくと安全の作業打合せなどに役立つので実施するとよい。
6)危険性又は有害性の特定
危険性又は有害性の特定を行う場合は、以下のことに留意する。
・対象作業取扱いマニュアルや作業手順書を用意する(それらがない場合は、作業の概要を書き出す)
・対象作業をわかりやすい単位で区分する
・日常の仕事とは違う目、すなわち危険がないかという目で、現場を観察してみる(過去に起こった災害は、そんなことが起きるわけがないと思われるような災害が多い)
・機械や設備は故障するし、人はミスを犯すということを前提に作業現場を観察してみる
・危険性又は有害性の特定に当たっては、これによって発生する災害について、次の「7)リスクの見積り」を適切に行うため、労働災害に至る流れを想定して「~なので、~して、~になる」という形で書き出すことが大切である。
7)リスクの見積り
特定された危険性又は有害性によって発生のおそれのある災害に対して、リスクの見積り方法に基づきリスクの大きさを見積ことになる。
リスク見積りにあたり、留意すべき事項は、次の通りである。
・リスクの見積りは、極力複数の人で実施する。多様な観点があった方がより適切な見積りができるからである
・リスク見積りのメンバーのリーダーは、必ずしも上位職の者とは限らない。作業内容を最もよく知っている人がなるのがよい
・リーダーは意見の調整役に徹するように努める
・現在行っている安全対策を考慮してリスクの見積りを行う
・リスクの見積りにあたっては、具体的な負傷・疾病を想定する
見積りした値がばらついた時は、よく意見を聞いて調整する(こうだと決め付けてはいけない。メンバーの経験、知識、年齢、性別等それぞれ違うので、バラつくのが当然と考える)見積りの値は平均点ではなく、多数決で決めるものでもない。グループで話し合い、合意したものとすることが大切である
・見積りの値については、説明のつくものでなければならない(やま勘は禁物である)
・過去に発生した災害の重篤度ではなく、最悪な状況を想定した重篤度で見積もる
・見積りの値はグループの中で、最もリスクを高く見積もった評価値を出した人からよく意見を聴き、メンバーの納得のもとに採用する
などになる。
これらの点に留意し、グループで意見を出し合い、話し合い、意見の違いについてはお互に調整し、最終的にはグループの総意として集約する。これらの過程により、情報や認識が共有化される。
事例】リスク見積りの方法(マトリクス法の例)
(1)負傷又は疾病の重篤度の区分
表1. に重篤度と被災の程度・内容の目安を示す。
表1. 重篤度と被災の程度・内容の目安
重篤度(災害の程度) | 被災の程度・内容の目安 |
---|---|
致命的・重大 ☓ | ・休業災害(1ヵ月未満のもの)、一度に複数の被災者を伴うもの |
軽度 〇 | ・不休災害やかすり傷程度のもの |
(2)負傷又は疾病の発生の度合の区分
危険性又は有害性への接近の頻度や時間、回避の可能性等を考慮して区分する(表2. 参照)。
表2. 発生可能性の度合と内容の目安
発生可能性の度合 | 内容の目安 |
---|---|
高いか比較的高い ☓ | ・毎日頻繁に危険性又は有害性に接近するもの ・かなりの注意力でも災害につながり回避困難なもの |
可能性がある △ | ・故障、修理、調整等の非定常的な作業で危険性又は有害性に時々接近するもの ・うっかりしていると回避できなくて災害になるもの |
ほとんどない 〇 | ・危険性又は有害性の付近に立ち入ったり、接近することは滅多にないもの ・通常の状態では災害にならないもの |
(3)リスクの見積り
重篤度と可能性の度合の組合せからリスクを見積る(表3. マトリクス法を用いたリスク見積表)
表3. リスク見積表
可能性の度合 |
重篤度 |
負傷又は疾病の重篤度 |
||
致命的・重大 ☓ |
中程度 △ |
軽度 〇 |
||
負傷又は疾 病の可能性 の度合い |
高いか比較的高い ☓ |
Ⅲ |
Ⅲ |
Ⅱ |
可能性がある △ |
Ⅲ |
Ⅱ |
Ⅰ |
|
ほとんどない 〇 |
Ⅱ |
Ⅰ |
Ⅰ |
(4)リスクの程度に応じた対応措置(優先度の決定)
リスクの見積りから次の表4. に示す通り、優先度が決定される。
表4. リスクレベルと対応処置
リスクレベル (優先度) |
リスクの程度 | 対応措置 |
---|---|---|
Ⅲ | 直ちに解決すべき、又は重大なリスクがある。 | 措置を講ずるまで作業停止する必要がある。 十分な経営資源(費用と労力)を投入する必要がある。 |
Ⅱ | 速やかにリスク低減措置を講ずる必要のあるリスクがある。 | 措置を講ずるまで作業を行わないことが望ましい。 優先的に経営資源(費用と労力)を投入する必要がある。 |
Ⅰ | 必要に応じてリスク低減措 置を実施すべきリスクがある。 | 必要に応じてリスク低減措置を実施する。 |
8)リスク低減措置の検討及び実施
リスク低減措置の検討を行う場合、法令に定められた事項がある場合には、それを必ず実施するとともに、リスクの高いものから優先的に検討を行うことになる。
その検討・実施にあたっての安全衛生対策の優先順位を図5. に示す。
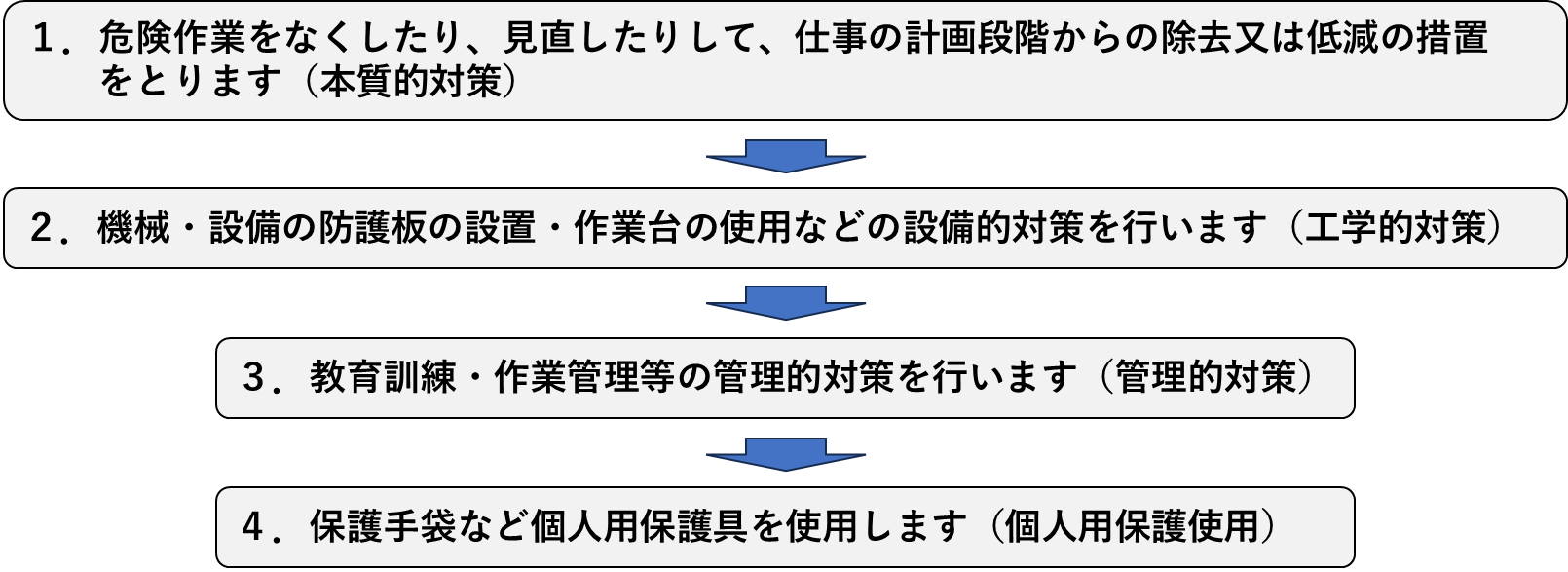
図5. リスク低減措置の検討及び実施の流れ
リスク低減措置の原則は、まず危険作業をなくしたり、見直したりすることでリスクを減らすこと(本質的対策)を検討することである。それらが難しいときは、設備的対策(工学的対策)を検討し、さらに管理的対策を検討する。個人用保護具は最後の対策である。
次に大切なことは「リスク低減措置実施後の検証」である。目的通りのリスクに下がったかどうか
を、リスクの再見積もりで検証することは、リスクアセスメントの精度向上につながる。しかし、現状の技術上の制約等により、対応が困難な場合は、リスクが残り「残留リスク」となります。「残留リスク」については、「リスクアセスメント実施一覧表」の備考欄に記入するとともに、直ちに、作業者に対して「決めごとを守るべき理由」、「どんなリスクから身を守るか」等どのような残留リスクがあるかを周知し、「暫定措置」を実施し、設備改善等の恒久対策の検討・実施は、次年度の安全衛生管理計画などに反映させて、計画的に、解決を図ることが大切である。
9)リスクアセスメント実施状況の記録と見直し
前の段階で検討したリスク低減対策設定後に想定されるリスクの再見積りの結果について、リスクアセスメント担当者等(又は安全衛生委員会等)による会議で審議し、事業場としてリスク低減対策の実施上の優先順序を判断し、具体的な活動へ進める。
また、リスクアセスメントの実施結果が適切であったかどうか、見直しや改善が必要かどうかを検討し、次年度以降のリスクアセスメントを含めた安全衛生目標と安全衛生計画の策定、さらに安全衛生水準の向上に役立てることが望ましい。リスクアセスメント実施一覧表は実施記録として保存することが重要である。
2.食品製造業における機械設備のリスクアセスメント事例
平成 23 年度 中小零細規模事業場集団リスクアセスメント研修事業「リスクアセスメント実施事例集」株式会社インターリスク総研(厚生労働省委託事業)P 8 ~ P13 引用転載。
食品製造業における機械設備メンテナンスの事例を最後に紹介するので参考とするとよい。
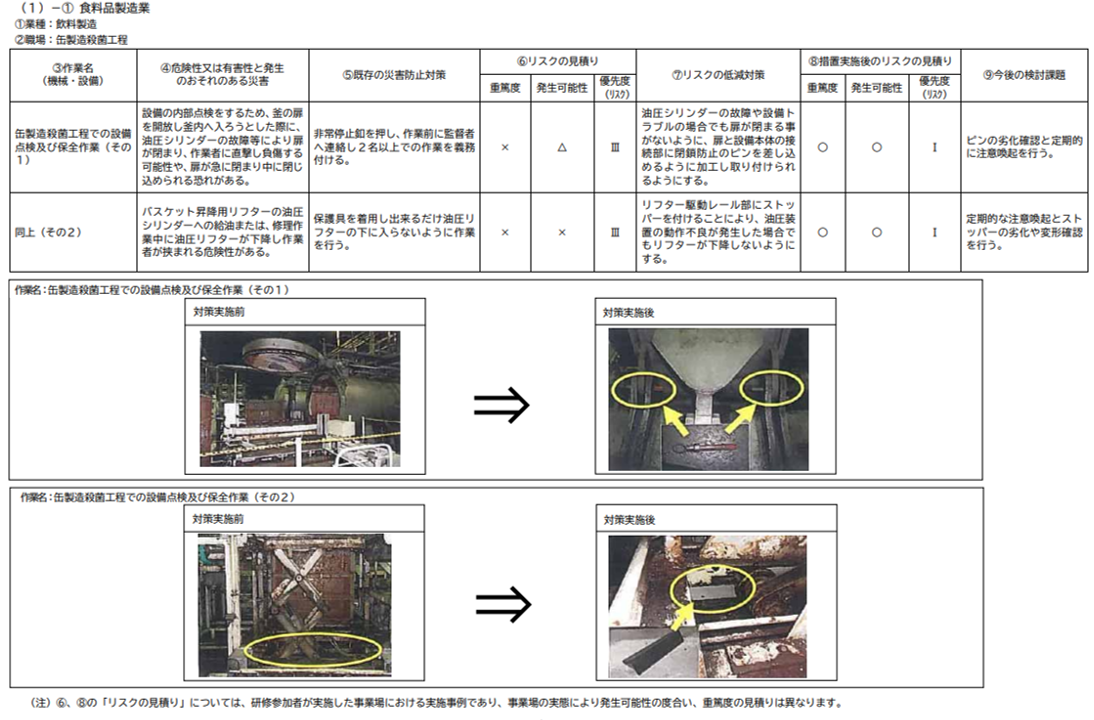
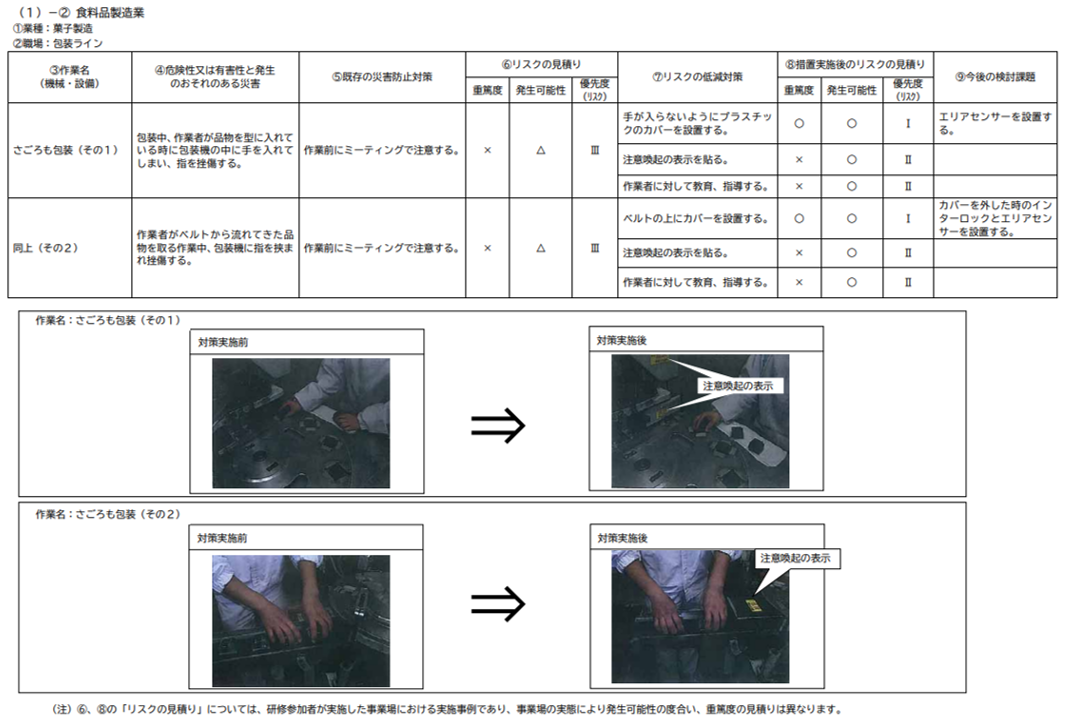
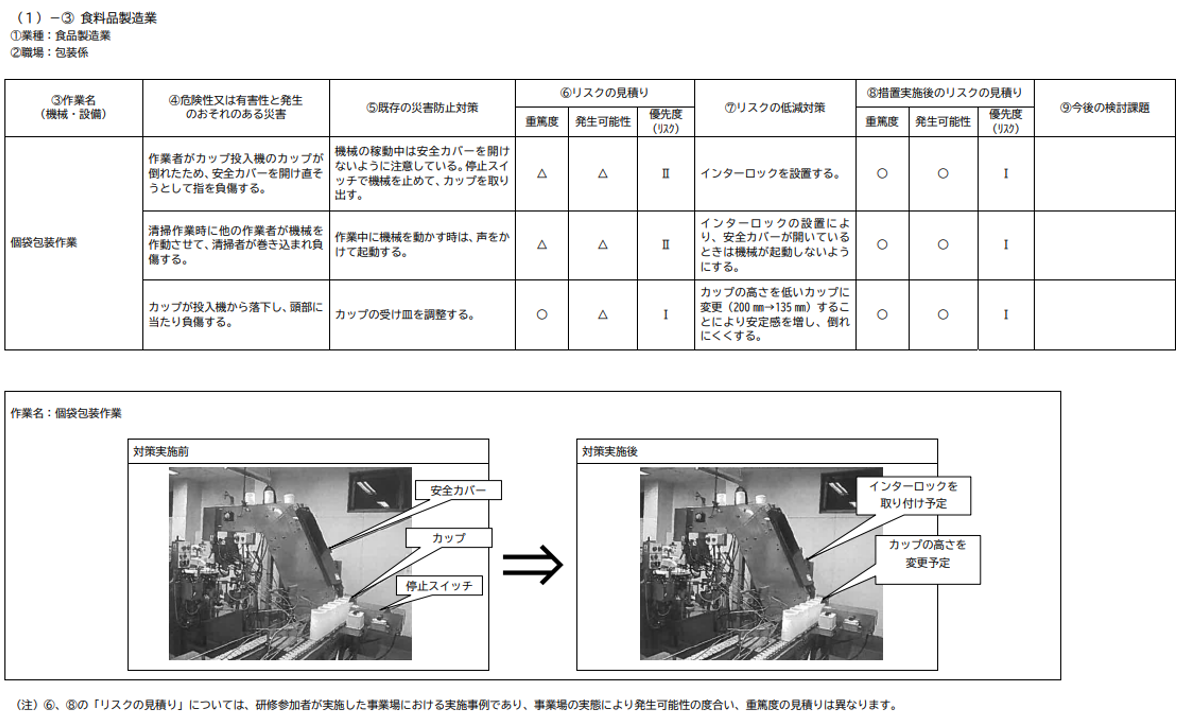
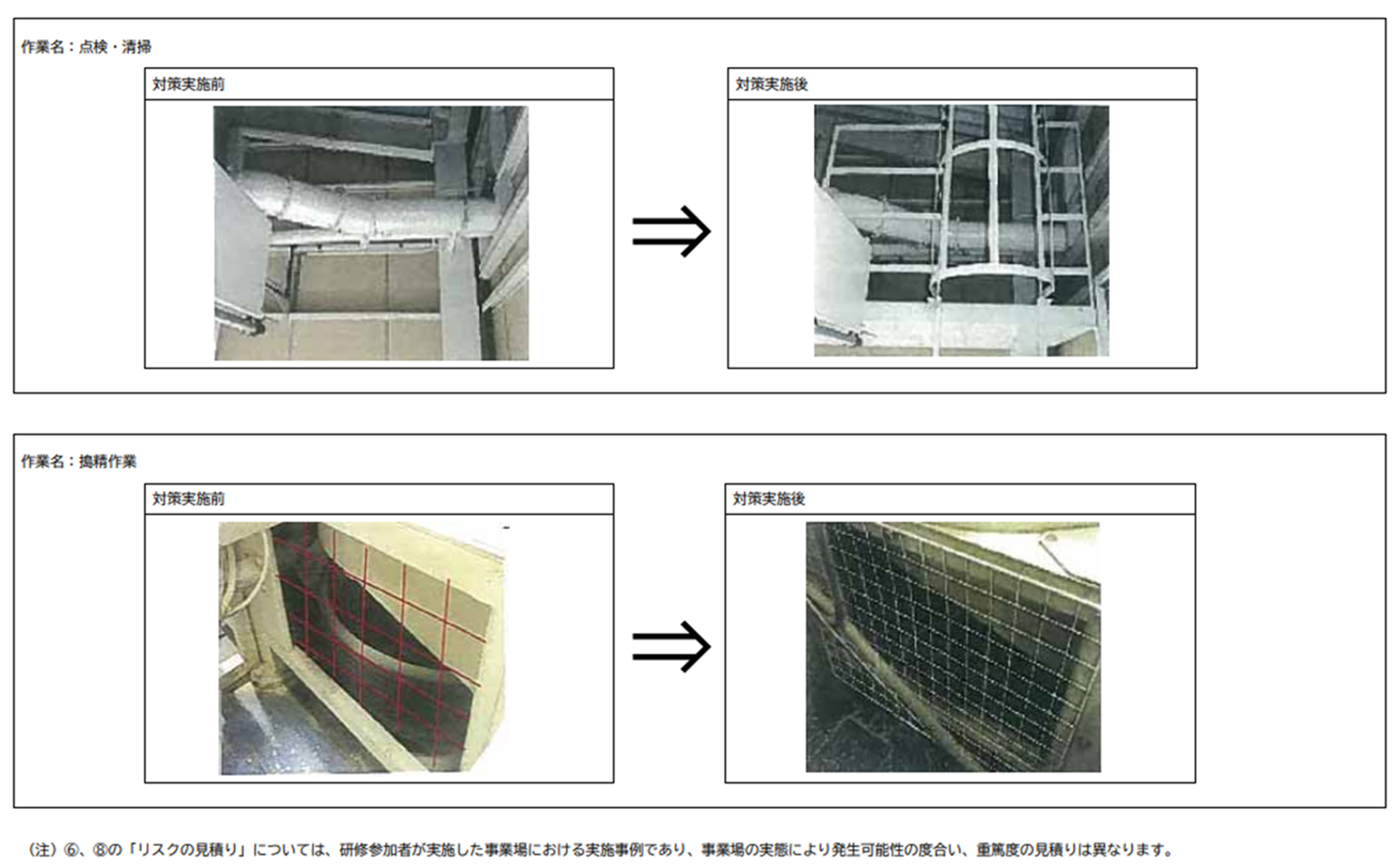
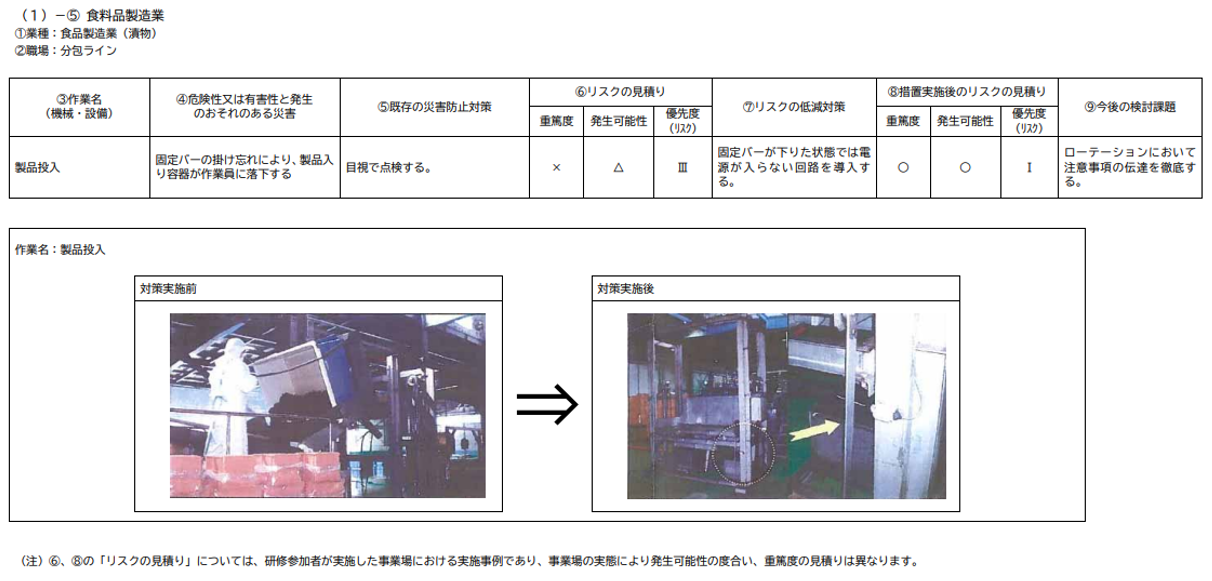
【引用先】平成 23 年度 中小零細規模事業場集団リスクアセスメント研修事業
「リスクアセスメント実施事例集」株式会社インターリスク総研(厚生労働省委託事業)P 8 ~ P13
以上
【参考引用先】
1. 厚生労働省:「リスクアセスメント等関連資料・教材一覧」
https://www.mhlw.go.jp/bunya/roudoukijun/anzeneisei14/
2. 株式会社インターリスク総研:「リスクアセスメント実施事例集」
https://www.mhlw.go.jp/bunya/roudoukijun/anzeneisei14/dl/130316.pdf