2023/08/21
『食品製造プロセスでの自動化構想立案の基本的な考え方』
Basic concept of automation concept planning in food manufacturing
process
1.はじめに
食品工場の製造プロセスを大別すると次の4つのブロックに区分することができる。
(1) ブロック1:「原材料受入れ保管」
(2) ブロック2:「製造・加工(素材型:混合型ライン)」
(3) ブロック3:「充填・包装・出荷」
(4) ブロック4:「ユーティリティ」
この4つのブロックは相互に関係するが、内容が大きく異なため、それぞれ区分して自動化および管理の対象を検討し、総合的に集約するのが望ましい。ただし、原材料受入れ、製品出荷は工場内の物流管理として、例えば、保管、在庫管理など共通部分があるため合わせて検討するのが良い。また製造・加工工程は、素材型ラインと混合型ラインでは本質的に自動化の対象が異なる部分が多いことから、検討対象が異なってくる。図1.
にFAのための自動化、管理対象の例を示す。
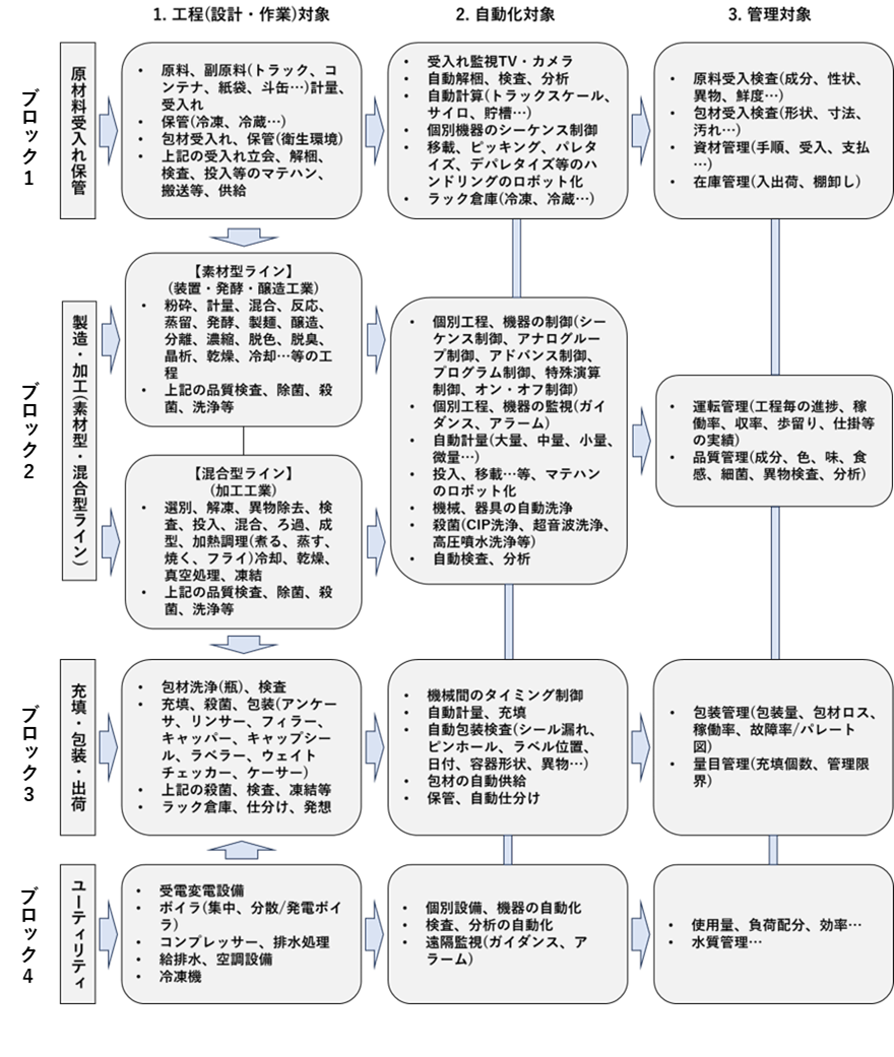
4つのブロックをそれぞれ細部の工程に分け、そこで自動化および管理の内容と、FA化を実施する範囲(キーテーマ)を明確にし、工程別の構想に落し込む必要があり、最終的には基本構想としてまとめる。
2.原材料受入れ保管
このブロックでのキーテーマは、『在庫品、仕掛品のゼロ』がポイントになる。
原材料受入れ保管は、一般の工場では調達部門が担当し、川上の原材料受入れ、保管、時には、原材料を製造現場へ供給している。また工場の規模によって異なるが川下にあたる製品保管、仕分け、荷揃え、出荷などを含め調達部門が担当しているケースもある。このように、このブロックは工場の[物流作業]、[物流管理]を担当しているといえる。
FMS化を指向している生産システムにおいては、製造に必要な原材料はその都度受入れ、出来上がった製品は直ちに出荷し、在庫、仕掛りをゼロにするのがゴールである。最終的にはこれを目指すにしても、現段階では現実的な基本構想を立案することになる。
何を、どれだけ生産するかといった基本条件から、工場内で扱う原材料がどのようになっているのか明確にしなければならない。事前に確認を行う作業であるが、例えば、原料、副原料などで明らかにする必要があるものとして、次のようなものが列挙できる。
(1) 品目毎の包装形態 (容姿、重量…)
(2) 月、週、日次などタイムフェーズに分解した品目毎の扱い量
(3) 受入れ形態 (人手、フォークリフト、コンベヤ)
(4) 受入れ検査、計量、受入れ窓口と伝票処理
(5) 格納、保管条件 (常温、低温)
などである。
さらに包装資材の種類、使用量などを明らかにし、このブロックの主な役割である「受入れ」、「保管」、「供給」に必要な機能は何か、その機能を満たすには、どんな設備が必要で、どんな工場レイアウト、設備レイアウトが最適か、などの基本構想を立案する。
このブロックの主な必要機能は、「保管機能」と「マテハン・搬送機能」で、次いで受入・払出、保管、製造に関する「計量機能」、品質、安全、衛生に関わり合う「原材料受入れ検査機能」などである。保管機能は『物を保管しておき、必要に応じて出す』ことであるが、これは経済的メリットがあるとき活かされ、必要な物を準備する時間、つまりリードタイムが短ければ不要とすることができる。従って、原料、包材など、納入先と納期を短縮する交渉は最も重要なポイントになる。しかし、どうしても必要な時に、必要な物を受入れたり、供給することが技術的にも経済的にも不可能な場合に、保管機能を持たせることになる。保管機能を持った自動化されたシステムが自動倉庫である。
自動化レベルから倉庫を分類すると、次の3つになる。
(1) 人力倉庫(ハンドリングを含め人間が作業)
(2) 機械化倉庫(ハンドリングにフォークリフトなどを使用)
(3) 自動倉庫
である。
自動倉庫とは、入出庫およびその周辺のハンドリングが自動化され、また関連する情報処理も自動化されている倉庫といえる。これに保管の物理的形態が立体化されたとき、これを立体倉庫という。
立体倉庫はJIS B 8940では、次の2つに大別されている。
(1) 建屋と分離してラックを組立てる小、中規模向けの「ユニット式(Free
Standing Warehouse)」
(2) ラックと建物が一体になっている中、大規模向けの「ラックビル式(Rack
Supported Warehouse)」
がある。
現在の自動倉庫は、これまでの保管機能に加え、FA化システムのサブシステムとして、物の流れのタイミングをコントロールしたり、物に対する情報を的確に把握し、原材料の適性発注、人的ミスの防止、工程間の受渡し調整など、管理効率向上に対して貢献度が大きくなっている。
自動倉庫を運用面から見ると、物が工場に入荷してから、自動倉庫に入れるまでの荷役、搬送作業と、入庫手続き(登録、処理)などを行う「入庫準備」、物が入庫し、格納棚に保管され、要求に応じて出庫される一連の「入庫・格納・出庫」操作、取出し(ピッキング)、行先別荷揃え作業、出庫手続きなどを行う「出庫準備」の3つに大別できる。特にこの中で入出庫準備作業をいかに早く、効率よくできるか、基本構想の立案がキーポイントになってくる。すなわち、降ろす、積む、横持ち、取出すといった荷役、搬送の自動化ができるかである。例えば、多くの実績のある産業用ロボットを利用したパレタイザ、デパレタイザなどの利用はできないか、また搬送に無人搬送車が利用できないか、人間が介在したとしてもハンドリングの機械化によって、省力化が可能にできないか、といったことが構想の対象となる。
これらのハンドリング・搬送構想を導き出す上で重要なことは、原料、中間製品、包材、製品などが設備との関わり合いの中で、物や人の動きがどのような動線を描くべきか、それぞれ物と物、物と人が交差、接近、接触などしていないか、十分な詰めが必要になる。完全無人化ができれば別として、通常、人間の介在が前提になってくる。従って、「物の動き」、「人の動き」を優先し、それらから設備(機械)レイアウトを導き出すことが重要なポイントになる。また原材料、製品などの搬入、搬出のためにトラック、ローリーといった運搬車の動き、工場内の駐車を含めた移動経路は理想的なものになっているか、さらに受入れた時から物に“付いている情報”受け取った後“付けた情報”は最後まで有効に活用できる『仕組み』を構築することである。
食品工場の受入れ作業者が専任になっていて拘束時間が不規則となっている現状を見かけるが、受入れ作業や帳票処理を含めた作業をFA化にどのように組入れ、システム化するかも重要なポイントになる。例えば、計量、手続き(伝票受入れ、処理)、荷役といった作業、すなわち、これらの無人入庫システムができないか、構想の段階で検討することも重要である。
3.製造・加工(素材型・混合型ライン)
このブロックでのキーテーマは、『混合型ラインの自動化』がポイントになる。
食品の製造・加工は、装置中心の素材型ラインと、食品加工機械を中心とした混合型ラインに分けられる。前者は少品種多量生産形態を取りながら、連続化を指向し、早くからPA(Process
Automation)を旗印に、自動化を進められ、省力化のレベルもかなり高くなっている。ところが後者の混合型ラインは以前から多品種少量生産を強いられ、それなりに自動化を進めてきたが、実態は人手に頼る部分が多くなっている。さらに近年の多様化対応で、ますます工程は煩雑化し、人手がかかるばかりである。両者とも多様化対応に苦慮しているのが実態である。両者にかかっているのは、製造・加工に柔軟に対応できるフレキシブルな装置、食品加工機械あるいは人間系、情報系を含んだシステム、つまりハードとソフトが一体としたFMSが望まれている。
ここで必要とされているFMS化を進める上で、確認しておきたい事項を述べる。大ロット生産を指向されていた生産方式を改め少ロット生産方式によってJIT生産を確立し、製造工程の仕掛り品、原材料、製品を含めてノンストック化を図り、期待する効果として、作業量の削減、多台持ち、冷凍・冷蔵などの保管スペースの極小化を図るなどしてQCDの向上を図って行くことである。ここで、主に混合型生産システムの基本構想立案にあたって、検討すべき項目について要点を列挙する。
(1)
設備を小型、小規模化し、製造ラインの複数化あるいき多系列化を試みる。ロットサイジングの設定および等量化、混流生産の可能性についても並行して検討する。
(2)
工程間および機器間を同期化(バランス)することによって、製造・加工品の工程持ちを少なくする。この要求を達成するためには連続化が欠かせない。工程持ちが発生すると、仕掛り品の山ができたり、作業の手待ちがでたり、想定以上のムダ、食品ロスにつながる。
(3)
工程間および機械間の連続性を向上させることによって、物の経路を適性化し、仕掛り品を必要最小限に抑え、作業の停滞やムダを無くす。ここでいう連続性とは、計量、粉砕、混合など工程の機能別連結というより製品系列による連結をいう。
(4)
粉体、液体、固体を問わず微量計量を含めた高度な自動計量システムを確立する。被測定物の種類、量によって、系列化できないか、例えば、微量計量、少量計量、中量計量、大量計量毎に系列化は可能か、自動化の範囲は、また累積計量(重ね合わせ計量)、累積分割計量といったように計量方法に工夫ができないか、などを考慮して検討する。
(5)
実用的な自動洗浄、乾燥システムはできないか、洗浄困難な設備の移送配管やシュートを止め“配管レス構造(パイプレス化)”にできないか、また機器の架台は洗浄の弊害となることが多いため、例えば、キャスター付き機器にして、洗浄専用設備を設け自動洗浄・乾燥エリアに移動し、洗浄処理できないか(段取りに手間のかかる機器については同一機器を2台準備し交互に洗浄する)、大型機器で移動が困難なものについてはCIP洗浄(定置洗浄方式)が採用できないか、基本的には室内を乾燥状態に保ち、濡らさずに洗浄する方法を構築することである。つまり、汚れを広げない、汚れるものを少なくする、汚れたところだけ洗浄、洗浄水の使用は極力抑える、といった基本に立ち返って考えることが最良である。
(6)
重要な標準作業化への取組みは、毎日の作業そのものが平準化されて初めて標準作業化が可能になる。標準作業は物・機械・人の動きを有機的に組合せることによって決まるもので、一般にいう食品製造・加工時の粘度、粒度、時間などを定めた作業標準とは異なり、作業条件そのものをあらゆる角度から徹底的に改善したものが標準作業である。理想的な標準作業を導き出すには、次の5つ(5W1H)を実践することが近道である。
① What(何を、どんな商品を?)
② Who(どんな人や機械で?)
③ How(どんな方法で?)
④ Where(どこに置くか? どこに運ぶのか?)
⑤ When(何時に、どのくらいの時間で、タイミングは?)
①~➄につきWhy(なぜ)を繰り返し追及することがポイントになる。
(7)
混合型ラインのFMS化で最も重要なのは、工場レイアウトである。レイアウトを考える場合、建屋が複数階に及ぶ「縦系列型」と平屋の建物あるいはワンフロワの「横系列型」に分けることができる。装置を主体にした素材型ラインは、一般的に縦系列型レイアウトが多い。これは物の移送が配管、シュータなどで容易にできること、また自動化が進んでいることもあって、縦系列型レイアウトでも、特に問題がない。しかし、混合型ラインや包装型ラインは搬送しにくい原材料が多く、食品加工機器間の連結が難しいこともあって、縦系列型レイアウトは多くの問題を含んでいる。従って、縦系あるいは横系いずれかの系列を選択するのか、慎重な検討が要求される。そのため次に列挙する検討項目を考慮する必要がある。
①
物と人の上下の移動による弊害、例えば、1階と3階の縦移動と平屋(平面移動)との対比で検討する
② 洗浄頻度の高い機器の扱い
③ 多台持ち(段取り…)作業の考え方
④ 機器の接近度、分散度(相関関係図表 / Relationship
Chartによる解析)適性化
⑤ 衛生面の考え方と方針
⑥
製造・加工作業の単純化と作業発生箇所の集中化、付帯作業(準備、洗浄、除菌…)のムダの排除
などである。図2.
に混合・包装型ラインのレイアウト例を示す。
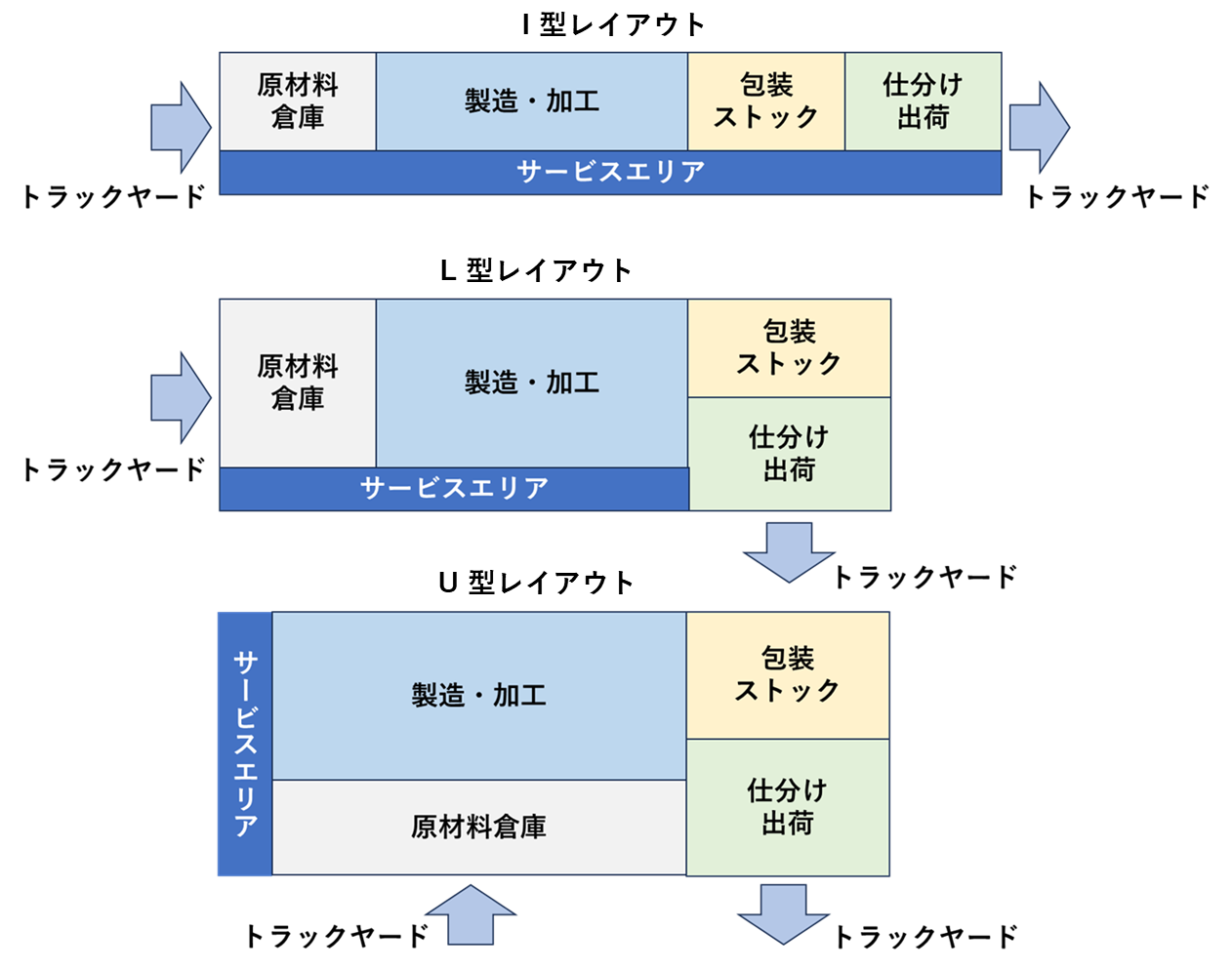
これは平屋の建物で、食品工場のレイアウトとして、ベストということではないが、工程間の連結性を高め、同期化を図るには同一階の横系列型レイアウトがベターといえる。これから少ロット化がさらに進むと、物の搬送回数の増加、洗浄、分析検査など作業が増え、当然、物や人の移動が多くなってくる。縦系列型レイアウトにすると、各階をつなぐ手段としてエレベータの設置が必須となり、物の移動が集中すると、自ずと限界が出てくる。従って、エレベータを利用する厳密なスケジュール管理が要求されることになる。ここで述べたレイアウトの決定はFMS化のキーポイントになってくる。
(8)
少ロット化が進むと、中間製品、製品などの成分分析や微生物(菌)検査が増え、FMSを構築する弊害になることがある。従って、迅速な分析システムについても、あらかじめ調査、検討の対象として加えておくことが肝要である。
上記8つの要点を詳述したが、この他にマテハン・搬送に関する構想の決定は、FMSの大きな評価対象になってくる。従って、ブロック1およびブロック3の個別構想と合わせて、一貫した方針の基に、基本構想を立案する。
4.充填・包装・出荷
このブロックでのキーテーマは、『機器の同期化』がポイントになる。
前述したように、充填・包装工程は包装準備・供給などの定常作業、トラブル処置、包装状態の監視作業のために、常時、数名のオペレータがラインに張り付き、拘束されている。従って、オペレータが拘束されずに、充填・包装ラインや、その個別機器を1人でどれだけ受け持つことが可能か、すなわち、ながら作業(作業をしながら別のことも同時進行で行うこと)によって、いかに『多台持ち』ができるかが勝負である。異常が生じたとしても、不良品の山をつくらず、1つでも不良品が発生したら取り除くことができれば、その可能性が十分でてくる。不良品が出たら、すぐ自動的に処置する仕組み、つまり機械故障や、製品不良を的確に検知し、状況に応じて自動停止する仕組みをつくることである。
充填・包装工程の各機器間、各作業者間はベルトコンベヤなどで接続されているケースが多く連結性は極めて高いといってよい。しかし、一般には充填機の速度が前提になって、次工程の包装や付属機器の速度バランスが決められ、それに合わせて、オペレータが配置されているのが現状である。従って、ラインや各機器間のバランス、すなわち「同期化」が最も重要なキーポイントになってくる。
一般の包装ラインは、図3.
に示すように製造・加工された粉体、液体、粘体…などの被包装物は配管ライン、ダクト、コンベヤ等を介して個装用充填機・包装機に供給され、中装機、外装機に接続されている。
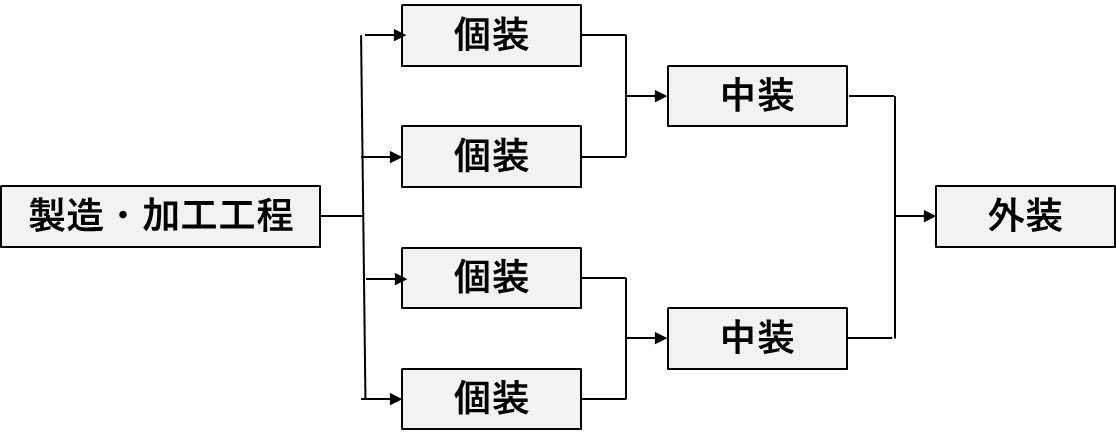
これらのラインは後工程になるほど作業サイクル時間が長くなり、ラインが兼用されるため、その台数が少なくなってくる。個装機は被包装物の形状、寸法の変更、また中装機、外装機は詰め数、まとめ数などの変更が容易にできなければならないし、種々の包装変更にも対応できることが求められる。さらに包材の供給、パレタイザ、自動倉庫との接続など一連の物の流れの中で、どの部分を自動化するのが効果的か、機器間の滞留、バッファの考え方など含めて十分な検討が必要である。ここで要求されるキーポイントは、フレキシブルな包装ラインである。
さらに付け加えると、充填機が高速であるがために、チョコ停の発生頻度が高くなり、稼働率を落として運転している状況も見られる。充填機を含めたライン速度の適性化と、作業形態から見た包装ラインの構築を立案することが重要になる。また、特別な場合で、準備作業、品種切替え、作業終了時に、その都度、充填機やラインの洗浄を実施するケースもある。これもゼロ段取りを目指すが、難しい場合はいかに短時間に洗浄できる方法を構築できるかがキーポイントである。手際よく充填機を洗浄するめために、作業の手待ち、重複作業を極力なくすといった取組みを考え標準化することである。
充填・包装工程で厄介な問題は、充填機で発生する4つの点にある。
(1) 充填量(中身)過不足
(2) シール不良(剥がれ、幅過不足、斜めシール、強度不足)
(3) 体裁(ピンホール、汚れ、キズ)
(4) 印字・捺印・日付不良(薄い、ズレ、不鮮明、汚れ、欠落)
などである。これらの異常検知は、ウェイトチェッカ、磁気センサ、光センサ、パターン認識、ビジョンセンサなどの各種技術を取入れることで解決できるようになってきている。
上述した充填・包装工程のFA化構想の立案のための要点を列挙する。
(1)
個装、中装、外装、各装置およびこれらに付帯する諸機器の組合せ、分業化の範囲、つなぎなどの検討から、連結性の最適化を行うことによって、同期化された包装ラインを構築する。ただし、ラインのコンパクト化(コンベヤを極力短くするなど)は基本になるので、作業面からのアプローチが最も重要になる。
(2)
拘束されている監視作業の排除、定常作業の削除を行うことによって、ながら作業を基本に、1人多台持ちを可能にする。そのためには、すべての機器について、物・人・機械の動きを有機的に組合せ実施できるようにすることと、それに伴うセンシング技術の確立、さらに目視検査に替わる自動検査システム技術を確立する。
(3)
チョコ停を含めたトラブルによる停止ロスタイムを削減し、稼働率向上に努めるとともに、目標として良品率100%を目指す。そのためには、トラブル原因のトップといわれる包材そのものと、包材供給装置などを構成する各機器の安定化の検討を行う。
(4)
個装段階で不良品を排除し、後工程に不良品を送らない徹底したフルワークシステムを確立する。
(5)
準備作業後、品種切替え、後始末などの時間短縮を図るために、ゼロ段取りの技術(ボトルなどを外さなくて済む切替え、部品の軽量化等)を積極的に取入れると同時に、洗浄の標準作業化を図る。
(6)
工程で、何が正常で、何が異常であるか、明確にするために『目で見る管理』を徹底させる。近年、IoT技術などの導入が進み現場に行って各機器を目視確認する頻度が減り、中央制御室などのモニターで常時ライン全体の運転状況、包材不足の予知、機器の異常、包装状態の異常などを遠隔監視できる技術が多く上市されているので積極的導入を検討する。
この他に、作業に関して述べると、作業の発生場所は極力集合させ、労働密度は高く、労働強度は弱くする取組みが重要である。この工程を無人化することの困難な理由は、被包装物、包装資材、包装機械の3つが相互に複雑に関連しているため、どれか1つ問題が発生しても影響が大きく、複雑化してしまう点にある。そのため優れた監視システム、自動検査システムの確立が重要になる。さらにこの工程は、衛生、騒音といった作業環境に配慮が必要で、特に衛生面を考慮すると、物や人の出入りを極力少なくしリスク低減を図る必要がある。
5.ユーティリティ
このブロックでのキーテーマは、『無人化』がポイントになる。
このブロックは、受変電設備、ボイラ、工業用空気源(コンプレッサ)、給排水、排水処理、冷凍機といったユーティリティ関連で、必要に応じて、法定でさだめられた有資格者を置き、運転、管理を行う必要があるため、保全部門などが主に対応している。ただし、近年では、人員確保が難しくなり、特に食品工場は、このようなユーティリティの管理を製造・加工部門が受け持つ傾向が強くなっている。
それは、ユーティリティ関連の設備や機器の性能、機能、信頼性などが飛躍的に進歩し、近年のIoT技術の進歩が拍車をかけ、遠隔監視システムが充実してきたことである。この中でもボイラに関しては個別機能はもとより、システムとして進歩し、省エネ、省力化が進んでいる。
混合・包装型ラインの食品工場は殺菌、加熱、保温などの運転状況によって蒸気の負荷変動が起こるため、ボイラの最適化は構想段階で検討しておく必要がある。また多品種、少ロット化が進むにつれ、食品工場の運転は現状に増して、変動が大きくなることを想定して既存設備の場合は、遠隔監視システムなどを付帯させるなどを考えることが大切である。
排水処理装置についても同様に高性能の設備が確立されており、監視システムを付帯することによって無人化が可能になることから、これらのユーティリティをFA化の中でどのように位置付け、システム化すればいいのか、を基本構想の段階で検討することが重要になる。
制御に関しては、それぞれの制御システム専門メーカーで構築されている個別制御システムを活かし、その監視、管理部分は、全体のシステム化構想に加味して検討することになる。基本的には情報を一元化し、全体の監視システムとリンクする全体最適化に向けた個別システムとの情報の授受ができることを前提条件として進める。
6.最後に
ここまで述べてきた基本的な構想立案に必要な考え方をまとめた。ブロック1~4について大まかな工程別構想が組立てられれば、工場全体の構想イメージができてくるので、自動化および工程管理、生産管理という観点から、もう一度工程の細部を検証・評価し、最終的な工場全体構想に仕上げることができる。
以上
【参考文献・参考技術レポート】
- 1.「食品工場のファクトリー・オートメーション」草間和彦 著 光琳
- 2.2023.05.22 技術レポート「食品工場における自動化 (FA化) に向けた考え方」木本技術士事務所HP https://www.kimoto-proeng.com/report/3440
- 3.2023.06.05 技術レポート「食品製造プロセスの自動化アプローチ」木本技術士事務所HP https://www.kimoto-proeng.com/report/3517
- 4. 2023.08.04 技術レポート「FA化推進チームの活動コンサル事例」木本技術士事務所HP https://www.kimoto-proeng.com/report/3602