2022/06/20
『食品産業の自動化による最新鋭工場に向けた今後の方向性について』
State-of-the-art factories and future directions through automation of the food industry
1. 食品産業(製造業)の抱えている課題
食品産業主に製造業においては適切な運用がされている工場が訴求すべき姿は「食の安全・安心の確保」と「コスト低減」が要求されている。また「働きやすい現場づくり」を支援するとともに既存工場における運用改善や課題解決に加え、新工場においては建設時の運用やシステムの検討など生産効率の良い全体最適化された自動化生産ラインの構築が各種手法を用いて構想段階から盛り込まれるようになってきている。
先にも述べたが食品製造業においては消費者からの要求で高い品質を満たすために安全・安心への取り組みが強化されている中でも徹底したムダの削減が求められる状況にあり、それに伴うコストの最小化が必須と考えられている。言い換えれば次の2つになる。
- (1) 商品品質の確保
- (2) 商品の低コスト
となる。
2050年までの約30年の間に労働力人口はどう推移するだろうか。現時点での想定では、3分の2にまで減少すると考えられていることから、食品製造業においては、今後人員不足となることが想像できることから、特に自動化設備に対する投資は増加傾向にある。
人海戦術的な人の力に頼る製造作業では将来生産が立ち行かなくなる可能性が高く事業そのものの継続も危ぶまれている。そのため近年、スマート化技術やIoT、AI、デジタルトランスフォーメンション(以下DXとする)を導入検討する工場が増加している。これらの技術を活用し、生産現場の安全性、製品品質とコスト競争力の向上を実現する計画・準備が必要である。それが主題である「スマート工場化」であり、その基盤となるのが「自動化」である。スマート工場化を構築する自動化については、直接並びに間接それぞれの作業において考える必要があり、ハードとソフト両面が一体となった自動化を目指すものになる。
食品製造業における自動化について解説する。
2. 製造現場をスマート化する自動化のKey Point
製造現場における自動化として次の3つがKey Pointにあげられる。
(1) 人手作業の自動化
製造現場作業には数多くの手作業が存在し、従業員に負荷がかかっている。機械化を推進することで、負荷や工数の削減と共に生産効率の向上も期待されている。自動化設備を導入したが思うような成果が得られなかったことで改善相談を受けた典型的な事例を紹介する。
ある製菓工場の工程カイゼン指導では、充填包装工程にある袋詰めの工程が人海戦術的な人手作業となっていたため、ライン内のボトルネックになっていた。中小企業向けの補助金を使って自動包装装置をラインに導入すると当該作業の効率はアップした。しかし運用を開始してみると中間品の供給、包装材の供給さらに包装を完了した袋を段ボールに梱包する際に、従業員が必要となっている状況が発生していて、人手作業が減ることがなくボトルネックの解消となっていなかった。このような結果となった理由は、自動化する工程前後の「物の流れ」ならびに「作業の流れ」を考慮せずに自動化装置を導入してしまったことによる。装置本体は自動化されていて個別には最新鋭であったが前後の工程を含めた全体最適化が欠けていた結果であることを診断結果として提示した。
また別の調味料工場では原材料の小分け計量作業を人手で行っていたが自動化設備を導入し従業員削減を図った。しかし毎回人手で計量値を設定する作業が必要な設備であったことから、時にはヒューマンエラーが発生する頻度が増加し、実績を記録する手間が増えていた。これは自動化設備への設定データ(IN PUT)や設備からの実績データ(OUT PUT)の情報の流れが自動化できていなかった点にあった。商品ラインナップに紐づいたレシピごとの小分け計量データのデジタル化(AIの活用など)を導入し、商品を指定することで自動計量設定ができる改善を行い、専門技能を必要としないことで操作を簡素化して行えるようにした。
これらの事例から見えてくる問題点は、次の2つに集約することができる。
- ① 設備単体の自動化
- ② ライン全体の自動化
であるが、①は個別に最適化された設備で単体としては最新鋭であり、➁はライン全体を最適化した工程の組合せでそれぞれ設備の能力が前後の工程と連動して最適化することにある。
機械化やロボット化による設備の自動化は有効な手段であるが、製造ラインの自動化とは人手を介さずに物や情報が一気通貫で流れることが必要である。個別に単体最適化された機械化やロボット化を進めてもボトルネックが変わるだけである。製造ラインの自動化構築では全体を見てライン検討を行うことが必要である。
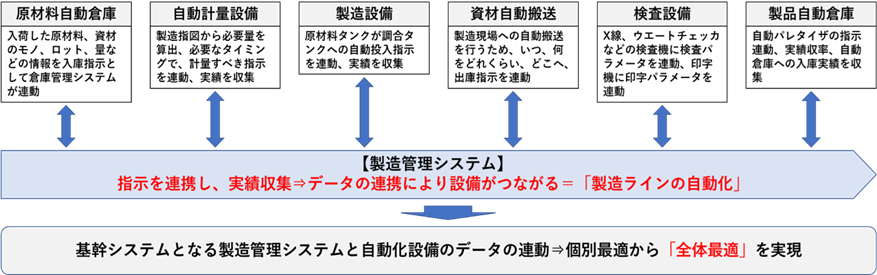
前述した調味料工場の事例では、小分け計量作業のみではなく製造工程全体を管理する製造管理システムを導入したことで、自動化設備と指図指示と実績がつながり工程前後の一気通貫製造ラインとすることができたことにより、従業員への作業負荷、工程間でのムダな工数を削減することができるようになった。
すなわち、これらの事例のように生産全体を管理する製造管理システムのIT化、自動化設備のデータ連動によって個別の部分最適化ではなく工場全体の最適化を実現してこそ、自動化装置・設備の能力や導入効率を最大化することができる(図1.)。
(2) 製造ライン検査作業の自動化
製造ライン自動化構築に伴いライン内の検査作業について考えてみる。工程間検査、最終製品検査など取り扱う製品によって異なる作業があるがここでは共通に導入されているであろう金属検知機、X線検知機、ウエイトチェッカなどの主な検査装置・機器があり個別には自動化が進んでいるが、異物混入を防止する目的で製造ライン上で検査員が目視で検品作業を行っている現場もいまだに多く見かける。ここでの問題点として特に特定の検査員のスキルへの依存負荷、疲労での集中力低下による品質精度のバラツキが発生するリスクが高くなることである。近年は画像処理技術の向上が図られ検査工程についても大きな進化が見られ、AIや深層学習などの活用が盛んになっている。
食品工場では、大きさや色調だけでは判別できないような画像処理では、2次元データだけでなく複数のカメラを配置しての3次元画像から得られるデータも組み合わせて総合的に判別できるようになってきている。
従来用いられてきたルールで行う閾値処理などの画像処理では、正常品をNGとしてしまう過検出の発生やパラメータ調整の限界が自動化導入の障害となっていた。検査員である人間が経験を積んで学習するのと同様に、AIが入力されたデータを経験値としてパターン化し学習する深層学習を活用することで、熟練検査員が行っている目視検査を自動化することが可能になる。
良品と異物の差が少ない場合や、状況により良品と不良品の色調が変化するような場合には、高精度スペック(近赤外光利用など)のカメラを導入し対象物の材質が分かるようになる。野菜や果物、乾燥麺などでの異物検出、焼成食品、揚げ物食品などの焼き色の均一化、食品自体の傷み度合いや鮮度の把握などへの導入が近いと考えられている。
(3) 生産業務の脱属人化
労働人工の減少と技能継承の観点から、自己流や属人化からの脱却は自動化を進めて行く中で今後重要な取組みの1つになると考えられている。属人化は多くの工程で発生しているが、生産計画立案業務および作業手順書(要領書)の標準化にフォーカスして述べる。
特に多品種少量の加工型食品製造業では、生産計画立案業務は個人に依存しいるケースが多い。食品製造業ではアレルゲン物質などの品質に影響を与える加工条件を考慮した製造順序、品種切替による型替えや洗浄などの回数頻度の削減、設備や人員などのリソースの最適化を熟練の担当者が考慮し計画を立案する。不測の事態や製造順の入れ替えなど経験値と知見を持った担当者でなければ対応できないといった属人化なども見られる。そのような担当者は休暇など取りづらいといった意見を聞く。
ある惣菜工場では担当者が1日かけて1週間分の生産計画を立案していたが、生産スケジューラを導入した結果スケジュリングが自動化され、人手作業は微修正(計画外の割込み生産など)を加える程度に軽減された。
また別の工場で計画変更が多いお弁当工場では、迅速な情報共有が必須であった。1人で抱えていた業務を、リアルタイム化されたガントチャートによる見える化、計画立案ルールや予実管理などのシステム化を行い、それらを迅速に共有化することによって脱属人化を可能にした取組み事例もある。このような具体的な取組みはシステムを導入すること以上に、製造工程間の制約条件を洗い出す最良の機会であり現状把握ができること共に改善箇所も見える化できることから技能継承にも有効である。またトレーサビリティの観点からも製造現場では原材料や資材が正しいか、期限切れになっていないか、正しい手順で作業が行われているかなどのチェックが頻繁に行われる。これら作業は自己流や属人化で行われていると不測のトラブルにつながるリスクが高くなる。
脱属人化するためには何が必要か。従業員の誰もが同じように作業ができるよう作業手順(要領書)を標準化し指導教育および訓練を行い周知徹底することが重要であり、その結果として作業品質の安定化につながる。さらに同じ目線で比較できるようになるため、改善検討にも有効になる。
原材料などの入荷から出荷までの現場作業指示をITツールの活用によるシステム化で、システムの作業指示に従って作業を行うことや、バーコード、QRコード、RFIDなどを活用した原材料・資材の各工程でのチェックが可能になる。その結果、人と人が行っていたダブルチェックを人とシステムで行えることになり、作業従事者を削減することが可能になる。
食品製造業に限られることではなく、これは各種製造業においても共通の課題と言える。熟練担当者がいないと何もできない、判断ができないという状況があるようであれば早急の改善がひつようであり、熟練担当者への依存や負荷を低減する方策を検討しなければならない。熟練担当者をサポートできるレベルの作業従事者を育成することも計画的に進められる環境整備も必要である。
3. 製造現場をスマート化するソフト(業務)改善のKey Point
ソフト(業務)面からのスマート化を考えるとKey Pointは、次の3つがあげられる。
(1) 突発的な故障の起こらない作業環境の構築
食品工場における製造ライン停止は避けなければならない。製造ラインを構成している設備保全に課題を抱えている相談も非常に多い。生産性に直結する稼働率に最も影響を与えるのは製造設備であるが、多くの食品工場では故障が発生してからの事後保全対応での対応となっていることから、故障原因の確認作業に手間がかかっていて現場対応に苦慮していると聞く。大手食品工場では、保全を専門とする工務部門があるが、中小の食品製造業においては製造ラインの担当者が保全に関わっている状況が多くなっているのが現状である。この課題に対して製造設備保全の事後保全から予防保全さらに予知・予兆保全への支援・アドバイスを行う場面も増えてきている。
突発的な故障が発生しないように、まず予防を前提とした取組みを行ったうえで作業環境の構築を考えることになるが、製造現場の各種コントローラによる機械学習を活用した自動解析、予兆のリアルタイム監視を行っている。製造設備の稼働状態を把握する目的で温度や電流値、振動、異音などのデータを収集し、コントローラ内部でリアルタイムに診断、正常な適正レベルのモデルと比較することで故障の予兆を検知し、メンテナンスが必要なタイミングで自動的にアラームを出すことを可能にしている。この仕組みでは、情報を収集し、解析から診断までエッジ(装置や端末の近く)で実施することで、異常の兆候を検知することで、診断まで段時間でできるようになった。近年では遠隔での監視もできるようになっていたことで、遠隔での指示や支援も可能となった。解析診断の最終結果を上位システム(クラウドサーバなど)に転送するなどによりデータ容量も削減できる。
さらに機械学習を活用して、正常に稼働しているか適正な状態を学習させることを日々行うことで、その適正な状態から外れた不適切な状態を検知して、予兆として警告アラームを発することで自動的に製造設備を監視することを実行するシステムを構築できる。次のような問題点が機械学習を導入することで解決することができるようになる。
- ① 故障が発生するまでデータが取得できず閾値の設定ができない
- ② どこか壊れるまで予測ができない
などを解消できる。
この予知・予兆検知能力は経験値の豊富なベテラン保全担当者に頼るところが多く、ベテラン担当者が退職や定年といったことで不在となった場合、立ち行かなくなる恐れがあるため技能継承が急務になっている。
予知・予兆保全に必須な作業として、次の2つ項目について取組む必要がある。
- ① 適正な保全基準を決める
- ② 点検箇所・項目を具体的に決める
これらは、日常の保全業務である故障履歴、点検記録、保全記録など、個別に管理されている紙帳票やExcel書式に記録されていることが製造現場では多く見られる。ITツールを上手に活用して保全管理のシステム化が必要であり、個別の機器類をマスタとしてデータを紐づけ、保全記録を登録し、保全データを一元管理することで可能にしなければならない。そうすることで適正か、不適切か、あるいは正常か、異常かを判断する故障予知・予兆を考えることができ機械学習により警告アラームの自動通知ができるようになる。
この判定基準となる考えには定量的な閾値を設けて情報を共有し故障解析を行うことで保全基準の見直し、例えば故障解析、保全基準の見直しその後、予防・予兆保全の実施といった一連のサイクルが構築でき、さらに改善に役に立つことから、製造設備トラブルによる機会損失を無くすことができて、稼働率が向上し、作業品質・製品品質への効果も期待できる。
また予防・予兆保全は適正な保全サイクルを見定めるのにも有効となり、故障を防止するだけでなく、過剰な予防・予兆保全を防止することでムダの削減、コスト低減にも有効である。予知・予兆検知により修理準備や日程調整など必要なタイミングをその場にいなくても遠隔で把握、監視できれば、突発的なトラブルに対しても状況を把握して迅速な対応と現場担当者に指示することが可能となる。
(2) 製造現場におけるペーパーレスによる作業環境の構築
食品、医薬品ならびに化粧品といった三品産業の工場においては、異物混入リスクの観点から外部から製造現場に紙や媒体を持ち込まないことが推奨されていることからペーパーレス化も重要な取組みと考えられている。
紙の運用は記入の手間がかかり、帳票の回覧にも時間を要してしまっている現状がある。転記ミスや誤記のようなヒューマンエラーへの対策も必要なうえ、作業中に記入するため読みづらいなどミスを誘発するリスクが潜んでいる。
ペーパーレス化することにより作業実績などのデータも電子化されることで、手書きや回覧といった時間を大幅に削減ができる。実績集計も不要となり、日報作成の工数削減につながり、データの蓄積が進むと精度の向上や業務の効率改善が可能になる。蓄積された現場の生データ(電子データ)は「現場カイゼン」するための現状把握の材料になる。
ペーパーレス化することによる効果について考えてみよう。どのようなことにつながるかであるが、基幹システムと紙で運用している現場は、システムの計画と現場作業の実績とは差異が生じることから、人が作業指示を分解、記録、回収、集計、転記するといった業務が必要となっている。この状態では適切なマネジメントを行うことは困難である。
基幹システムと製造現場の計画に基づいた予実管理の差を製造管理システムでカバーすることで、各工程におけるシステム間の連動を自動で行い、製造現場で作業確認を行うことで実績を自動的に送信することを可能するこのように基幹システムへリアルタイムに連動をすることで、現場で収集されているデータを則活用して製造計画に反映させることができる。食品工場などでは、ペーパーレス化による記入・入力工数、回覧工数が削減され、データの精度が向上されることで、トレーサビリティの精度・追跡といった能力アップも同時に図れるメリットもある。
(3) 製造現場から得られる各種データ収集の自動化
製造ライン管理者が現場に行かないと作業状況や進捗が把握できない、生産計画立案に必要な稼働データを間接業務のメンバーが帳票を集めて判断するといった問題点が顕在している現場を中小製造業においては“お困りごと”として相談を受ける。製造ラインに設置されている現場機器類の稼働データを集約し、リアルタイムに集中管理・監視することで、現場に行くことなく迅速な状況判断が可能になる。さらに作業品質、製品品質や履歴データを管理することで、品質の確保だけでなく品質保証にも水平展開できる。
製造現場の作業カイゼンにつながることを前提に設置するカメラの映像データも紐づけてチェックできれば、現場に行って対応していた移動のムダ、作業のムダが無くなり、迅速な判断も可能になる。人が現場に入らなくてよくなることから外部から持ち込まれる異物などのリスクもなくなるので品質への懸念が軽減される。その上現場のフードディフェンス(FD)にも有効になる。すなわちこのような取組みを実行することによって、食への安全・安心をアピールすることができる。
複数の稼働データをリアルタイムで監視できる環境が構築できれば、迅速に稼働状態、進捗状況、作業状況を正確に把握することができることから、品質検査データの閾値との差異やバラツキが見えてくるメリットが大きい。従業員が集中管理室で製造の進捗や機器類の稼働状態を監視・管理することがかのうになれば、製造現場における確認作業の時間を削減でき、その時間を活用して改善検討など付加価値を創出できる現場体質にすることが、生産性向上に寄与することにつながる。中小製造業の加工型食品工場においては、一気に集中管理を行うのはハードルが高く困難が伴うので、ボトルネックとなっている工程を段階的に実現できるように工場診断を行い、実現に向けた支援・アドバイスも行いお手伝いをしている。ありたい姿としては、知見を持ったメンバーが本社や他の工場から生産拠点の稼働状況をリモートで監視し、トラブルや不具合に対しては遠隔で支援あるいは操作できる仕組みを構築することが望ましい。
ウエアラブル端末などを活用して稼働データを確認することを可能とし、実際の現場の状況をカメラで映像として配信しながらベテラン担当者、知見を持った担当者などがそれぞれの場所から支援・アドバイスができたり、機器類に端末のカメラを向けると画面上にAR(仮想現実)で対処方法が映し出されたり、対応マニュアルを映すなど後方向でのコミュニケーションも取ることが可能になる。
このような管理システムが構築できれば、国内外での対応もできるようになり有効なツールとなり得る。
4. 自動化による最新鋭工場とするための今後の方向性
製造現場の稼働データなどその他の各種データを活用する現場作業の効率化、品質確保への取組み、迅速な対応、意思決定支援といった仕組み構築について詳述したが、人手を介したカイゼン活動には限界があるので自動化の導入は必須となることが理解できたと思う。
自動化された最新鋭の工場はどのようになるのか考えてみよう。ありたい姿としては、自動化された工場が常に自動的に最良の状態に改善されることである。工場自体が自律化して良否判定、意思決定が自動的に行われる未来工場である。工場における自律化を定義づけすると次のように考えられる。
自律化とは、安全性をシステムが保証し、オペレーション自体は機械やロボットが自動で行い、常に最良の調整が自動で実施され、予期せぬ事態にも人の介入なしに対応できる工場となる。では、現在の自動化を考えた場合、一連の作業タスクには人の介入による対応が必須である。安全の保証やオペレーションをするのは人であり、予期せぬ事態には人が介入している。意思決定・判断においてはベテラン担当者や知見者が現場からいなくなっている現状を考えると人の介入は困難となっているので自動化への移行は必須と考えるべきである。
工場の自動化から自律化への移行をどのように推進し最新鋭工場とすればよいかである。
すなわちヒトを介さずに最良の調整が自動で行えるようにすることになる。製造現場のデータ、多くの情報を高度に解析して活用していく必要があり、そのためにはデジタルトランスフォーメンション(以下DXとする)に取組む必要がある。工場の製造ラインにおける自律化の有りたい姿を具体的に解説する。
例えば、製造中の稼働データと品質データを自動的にモニタリングしながら、設備ごとに稼働パラメータの調整を自律的に行わせるシステムとする。
従来はサンプル検査を行い、検査結果の状況と稼働状況を作業担当者が判断して前工程側の稼働パラメータの調整値を決定し、作業担当者が手動で稼働パラメータの設定を変更していた。自律化した工場では稼働データと品質データのモニタリングをリアルタイムで行い、自動調整するパラメータをAIやIoT、ICTなどの技術を導入し、システムと連動で製造設備へ適正パラメータを自動でフィードバックする高度な活用が自律化を可能にする。
その他のデータとしてエネルギー予測から設備稼働方法や稼働パラメータを調整することや、故障予測での事前検知により生産計画立案を自動で変更することも可能になることでエネルギーの需要供給のタイミングを図ることも省エネルギー対策にもつながる。
このようにデジタルデータを活用して業務を変革することが、メディアなどで頻繁に取り上げられているDXである。現在食品産業においても各種DXへの取り組みが検討されている。それに関連してIT、IoT、センサ、そしてAIを導入した多くのツールもあり、それぞれの強みのある領域も違があるので、ベンター選定についても迷うことが多いという相談を受けている。またDXツール導入にあたってはデータを収集して何に活用したいのかである。現状の改善につながる取り組みには必然的に目指すべき目標を設定する必要がある。期待すべきありたい姿は何かである。
自動化設備や自動化システム、IoT、AIといった手法は手段の1つであって目的ではない。主役となるのは業務の品質確保であり食品産業においては、安心・安全が必須でありその上で生産性が向上されるための製造設備の全体最適化、ここの業務担当者の変革と言ってよい。最適化構想を練るためには現在の問題点を洗い出し、課題を抽出し、その根本が何かを十分整理し、3年後、5年後、さらに10年後のありたい姿を描くことが望ましい。
自動化にはいろいろなアプローチの仕方があり、食品製造業についても素材型食品メーカーと加工型食品メーカーとでは、おのずと取り組み方が異なってくる。まずは、ボトルネックとなっている部分から自動化を検討し、着手されることが好ましい。
自動化から将来の自律化に向けた検討に向けて第一歩を踏み出すことである。製造ラインにIoTやAIが組込まれた自動検査を設置してみる、あるいはデータ収集システムを1か所設置してみて1工程の記録を自動収集できることで何がわかるか調査することから始めてもいいだろう。また、自分たちだけで何とかしようとせず知見を持っている専門の有識者などに相談することも推奨する。
最後に
「DXは単なるデジタル化ではない」ということを再認識しておくべきである。経済産業省は、2018年12月に発表した『DX推進ガイドライン』において、DXを「企業がビジネス環境の激しい変化に対応し、データとデジタル技術を活用して、顧客や社会のニーズを基に、製品やサービス、ビジネスモデルを変革するとともに、業務そのものや、組織、プロセス、企業文化・風土を変革し、競争上の優位性を確立すること」と定義づけている。つまり、DXの本質的な目的は「トランスフォーメーション(変革)による競争優位性の確立」であり、「デジタル化」はそのための手段と捉えるべきということである。
以上
【参考文献・引用先】
- 横河電機(株)HP 2020年9月16日発表 プレスリリース
「産業における自律化の調査を実施-プロセス産業の3分の2が2030年までに完全自律操業を見込む」https://www.yokogawa.co.jp/news/press-releases/2020/2020-09-16-ja/ - 農林水産省食料産業局「食品産業生産性向上のための基礎知識」
https://www.maff.go.jp/j/shokusan/sanki/soumu/seisansei.html - (株)日本能率協会コンサルティング「食品製造業の生産性向上事例集」
https://www.maff.go.jp/j/shokusan/sanki/soumu/attach/pdf/seisansei-7.pdf - 経済産業省「DX推進ガイドライン(2018年)」
https://www.meti.go.jp/policy/it_policy/dx/dx_guideline.pdf