2022/01/07
『炭酸飲料の製造法に必要な基礎知識』
Basic knowledge required for manufacturing carbonated drinks
1. 炭酸飲料の分類
炭酸飲料は、炭酸ガスを含有する清涼飲料の総称であるが、日本農林規格品質表示基準によれば(飲用適の水に炭酸ガスを圧入したもの、およびこれに甘味料、酸味料、フレーバリングなど加えたもの)と定義づけられており、図1.に示すような分類となる。
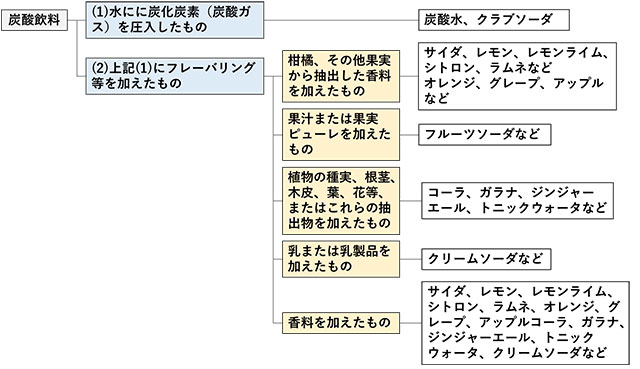
2. 炭酸飲料の製造方法
炭酸飲料の製造方法は、プレミックス方式とポストミックス方式の2種類があり、現在ではほとんどがプレミックス方式で製造されている。プレミックス方式とは糖液(シンプルシロップ)に酸味料や香料を加え調合液糖(フレーバードシロップ)をつくり、水と定量混合(プロポーショニング)したものを冷却し炭酸ガスを吸収させる方式である。一方ポストミックス方式とは調合糖液を一定びんに注入し、次いで炭酸水を入れ密封/密栓する方法である。
(1) 製造工程図
炭酸飲料の製造方法(プレミックス方式)の工程図を図2.に示す。
➢ リターナプルびん製品の工程
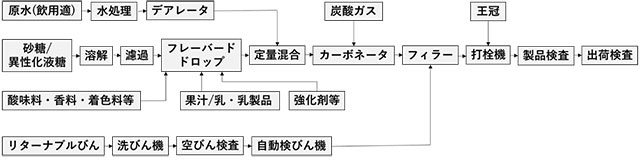
➢ 缶/PET/ワンウェイびんの工程
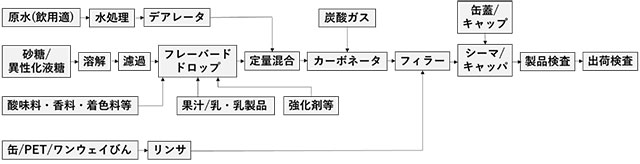
(2) 水処理
近年、原料水汚染の危険性が高まっていることから、水質の維持、確認のための日常管理および定期的な検査が重要である。
過去には、原虫(クリプトスポリジウム等)他に汚染されている危険のある原水に対しては、各処理工程を組み合わせた多段階処理システムなどが安全性をより高める意味からも有効なシステムである。図3.に代表的な多段階処理システムの工程を示す。
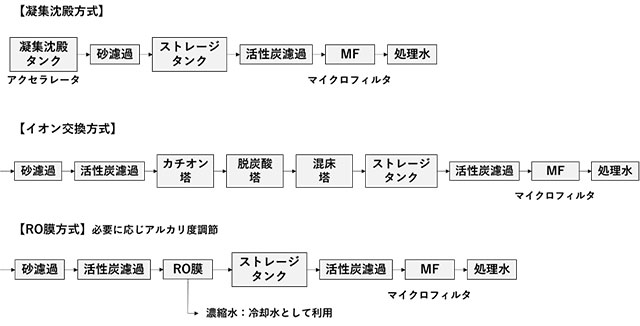
(3) シロップ製造
① 糖液(シンプルシロップ)の製造
シンプルシロップは通常、糖度(Brix)55度前後に調整される。これは、保存性を維持することと希釈時に取り扱いやすいためである。シンプルシロップ(Brix)最終製品のブリックスに応じてきめられるが、シンプルシロップの製造に際して重要なことは、原料配合表に基づいて水および糖類を正確に計量することが重要なポイントになる。優れた品質の糖液を使用し、衛生管理の行き届いた製造を行う限りにおいては、シンプルシロップの品質は安定であるが、溶解後はできるだけ素早く使用することが望ましい。
原料配合表に従って、規定量の水を正確に計量して溶解タンクに貯え、次に撹拌機を回転させながら糖類を規定量加える。固形の砂糖の場合には、通常20~30分間の撹拌で溶解できるとされている。この時の撹拌をあまり激しく行うと空気を巻き込んで好ましくないので注意する。
次に、シンプルシロップ中に混在する可能性がある微細な夾雑物を除去するためにろ過を行う。濾過は、通常、濾紙を有するフィルタープレスあるいは各種のカートリッジフィルターを通して行う。濾材の選択は、濾材の保留粒子サイズ、濾過速度、強度などの性能とシロップの性質を考慮して行うことが大切である。
濾過に際して、濾過助材を使用することがあるが、この場合粒子が微細で堅牢な珪藻土(セラミックスなど)が現在主流として利用されている。
➁ 調合糖液(フレーバードシロップ)の製造
➢ 原材料の配合
炭酸飲料の美味しさは、糖分と酸のバランス、製品それぞれ独特のフレーバーと色の組合せによってかもし出されている。炭酸飲料に使用されている原材料としては、酸味料(コーラ飲料のリン酸、無果汁フレーバー飲料や透明飲料のクエン酸、酒石酸など)、香料(製品の特徴を出すために、種々の香料が使用される)、および着色料(コーラ飲料のカラメル、無果汁フレーバー飲料の各種の着色料)がある。合成着色料も使用さるが、近年は、消費者志向に合わせて天然着色料の使用が増えている。
これらの原材料は、原材料配合表(処方)に従って、それぞれ仕込み単位ごとの規定量を正しく計量して糖液(シンプルシロップ)に添加し、混合する。
➢ フレーバードシロップの製造
処方箋の原材料は、そのままシンプルシロップに投入するのではなく、いったん水に溶解し、濾過、あるいはステンレス鋼製の金網のスクリーンを通して添加する。撹拌機を回転させながら原材料を加えて、十分混合する。撹拌を高速にし過ぎると調合糖液(フレーバーシロップ)に空気が巻き込まれることがあり、後工程の炭酸ガス圧入の妨げとなったり、充填時に起泡(フォーミング)を生じたり、製品の酸化を促進する恐れがあるので、過剰の撹拌は避ける必要がある。
このように、つくられた調合糖液(フレーバーシロップ)は、充填工程に移されるが、製品の品質を保持する上で極力早期のうちに使用することが望ましい。
(4) プロポーショニング(定量混合)
プレミックス方式では処理水とフレーバードシロップを一定の比率で連続的に計量、混合する。その装置をプロポーショナといい、この操作(プロポーショニング)を行い、炭酸ガスの圧入を行い充填する。
① プロポーショナとその選定
プロポーショナは通常、デアレータ、冷却および炭酸ガス圧入装置と組み合わせて、各メーカーより販売されている。いずれもその性能には大差はないが、それぞれに特徴があるので、メーカー選定にあたっては、次のことに留意する。
- 使用するシロップの液性
- 混合性の安定性
- 運転操作の容易性
- 洗浄殺菌・保守の容易性
といった点を考慮に入れるべきである。特に使用する「シロップの液性」については、果汁入りシロップで繊維質(パルプ)を含有するものでは、機種によっては機構上適切でないものがあるので、装置選定にあたっては事前に製品液を実際に流してみて配管や機器などで閉塞など発生しないか確認することが望ましい。
➁ プロポーショナの特徴
一般的なプロポーショナの特徴として、始動、停止時の混合比で糖度に0.1~0.2%のバラッキが生じる機種もあり、精密な制御を要する場合には留意すべきである。また製品の種類によっては、昇温したアルカリ液または酸液による洗浄が必要となる場合が生じたり、このほか熱水、蒸気あるいは塩素水によるサニテーションを行う必要があったりするので、これに十分耐えられるものでなければならない。混合比に異常な誤差を生じると、短時間で多大な損害を被るので、運転中に何らかの不調が生じた場合は、ただちに自動停止するような安全機構を持たせることも重要な選定ポイントである。
製品の糖度を、一定時間ごとに測定して、フレーバーシロップと水の混合比に異常がないことをチェックする。プロポーショナの吐出量は、充填機の充填速度にバランスさせる必要があり、始動、停止の繰返しをできるだけ最小限にして、充填がスムーズに行われるようにする。さらにプロポーショナの摺動部の部品、オリフィス、制御弁に傷が付いたりすると混合比のバラッキが大きくなることもあるので注意が必要である。
(5) デアレーション(脱気)
カーボネーション(炭酸ガスを圧入)を効果的に実施し、また充填機でのフォーミングの要因を減少するため、カーボネーションの前工程で原料水および製品液体中の溶存空気はできるかぎり除去することが望ましい。この操作をデアレーションといい、その装置をデアレータ(脱気装置)という。
原料水のみを脱気するか、シロップと水の混合液にしてから脱気するかは、液体の性質と工程設計の方針にもよるが、混合液の場合はフレーバーの損失が考えられるので、原料水での脱気を行うのが通常である。デアレータには各種の形式があるが、いずれの場合においても、9.3kPa(700mmHg)程度に減圧したタンクの中に液体を薄膜状、あるいは霧状にして流下させるような機構になっているので、脱気効率はタンク内における真空度と気液の接触面積によって決まる。したがって、真空ポンプの保守を十分に行い、その性能を維持することが重要であり、液体の流量を必要最低限にして、接触面積をできるだけ大きくするよう調節することが大切である。デアレータには、運転の停止時に真空ポンプの油や吸引装置の循環水が本体内に侵入して、内溶液を汚染しないよう、安全装置として、逆止弁、トラップ、真空開放弁などがされているのが通常であるが、作動状況については日常的に点検をしておくことが望ましい。最近では、オイルフリータイプの真空ポンプなども各種ラインナップされているので選定時に考慮するとよい。
補足:技術レポート「食品製造向け真空ポンプの正しい選定方法」を参照
https://www.kimoto-proeng.com/report/1998
(6) カーボネーション(炭酸ガス圧入)
フレーバードシロップと水の混合液に炭酸ガスを圧入させて、炭酸飲料とするが、この操作をカーボネーション(炭酸ガス圧入)という。カーボネーションは、通常カーボネータという装置の中で、液体に炭酸ガスを接触させることによって圧入を行う。
① 炭酸ガスの溶解度
一般に、気体が液体に溶けるとき、一定温度において一定量の液体に溶解する気体の量は、液体と平衡にある気体の圧力に比例する(ヘンリーの法則)。清涼飲料業界では、標準状態(1気圧、0℃)において、飲料に溶けている炭酸ガスの体積の飲料の体積に対しての比を表したものを、ガスボリューム(ガス容)と呼んでいり、飲料中の炭酸ガスの含有量を表す単位としている。
➁ 炭酸ガスの圧入温度
液体への炭酸ガスの吸収は、温度が低いほど大きいので、カーボネーションを効率よく行うには、一般には、液体を10℃以下に冷却して圧入する。温度が高すぎると炭酸ガスの圧力は高まり、カーボネータや充填機の運転管理がし難くなる。また充填機の内圧も高まり、充填時にフォーミング(起泡)を生じることもある。フォーミングは炭酸ガスの損失のみならず、稼働率の低下を招き、また吹きこぼれた液体が巻締機(キャッパー)などの汚れの原因になったり、充填不良品を発生させたりする。逆に液体の温度が低すぎる場合には、冷却器の消費電力が増加する。特に低温充填製品の場合には、カートンの結露による濡れを防止するため、充填巻締め後に加温する必要があるので、必要以上の低温は好ましくない。
③ 炭酸ガスの圧入
一定の温度では、カーボネータ内の炭酸ガス圧力が高いほど、その吸収はよく、一般には、カーボネーションは0.098~0.392MPaの圧力下で行うが、製品のガスボリュームを一定にするためには、カーボネータ内の炭酸ガス圧力は一定に維持しなければならない。そのためには、カーボネータへの炭酸ガスの供給が連続して、十分に行われることが必要で自動圧力制御装置が正しく作動していることが不可欠である。現在では、純度が99.95%以上の良質の炭酸ガスが使用されているので、ほとんど問題がないが、それでも、シロップや水の中に存在する空気が混入する恐れがある。これらの空気は、運転を継続すると、カーボネータ内では、空気が液体に吸収されないまま残留、蓄積され、その量が増えれば、真の炭酸ガスの圧力は指示値との誤差になる。残留する空気は、このほか充填機におけるフォーミングを引き起こし、また缶詰め製品の場合には、そのヘッドスペースの空気量を増加させる原因となる。こうした問題を避けるためには、カーボネータの内部の空気を運転中に定期的に除去する必要がある。
カーボネータ内での炭酸ガス吸収は、温度と圧力のみで十分行われるとは限らない。炭酸ガスと液体との接触面積が大きく、また液体の撹拌が適切におこなわれるほど、ガス吸収は速やかに行われる。カーボネータ内部で液体を冷却板上に薄膜状に流下させたり、タンク空間部に霧状に噴出させたりするのは、いずれも気・液の接触を効果的に行うためである。一般に、カーボネータへの送液量を少なくすれば、単位流量あたりの接触面積が大きくなるため、炭酸ガスの吸収はよくなるが、カーボネータの処理能力にも関係するので、実際には、設計能力を目安として液体の流量を決め、最終製品のガスボリュームを確認しながら、冷却温度とガス圧力を調整する。
添付資料1. 炭酸ガス吸収係数(ガス容:gas volumeをいう)表を参考に添付しておく。
④ カーボネータの点検・保守
カーボネータの運転中のチェックは、最終製品のガスボリュームの検査のほか、装置の作動状況についても行う。すでに述べた冷却温度とカーボネータ内の圧力は、製品のガスボリュームに直接関係する要因であるので、特に重要で、自動連続記録することが望ましい。液体が直接接触する冷却板内の冷媒のピンホールなどによる漏洩は常に監視を怠ってはならない。また冷却機系の安全弁などの安全装置の作動確認は、安全確保の観点から定期的に実施し、冷却板に過大な圧力がかからないように注意する。
(7) 容器洗浄
炭酸飲料を充填する容器にはガラスびん、PETボトル、缶など各種の方法がある。ガラス瓶の場合は、回収再利用するリターナブルびんとワンウェイびんに分かれる。現在でもPETボトルが50%以上を占めているが、環境問題を考慮してPETボトルからアルミ缶やリターナブルびんへの見直しも盛んになっている。ここでは、現在も主流となっているPETボトルについて容器洗浄条件について概説する。
PETボトル容器内の洗浄はリンサノズルからのスプレーパターン、塩素水の圧力および水量によって決まる。したがって洗浄効果を確認しながら洗浄条件を決めることが重要である。
PETボトル使用に際しては、40~50℃程度の温水による洗浄と塩素水(1~3ppm)による洗浄の組合せまたは塩素水単独の洗浄により洗浄される。以下の表1.に洗浄条件の事例を示す。
洗浄項目 | 洗浄条件 | |
---|---|---|
1.リンス水圧力 | 0.1961MPa以上 ただし、0.1961MPa以下であっても、リンサの洗浄効果が確認されている場合は可となる |
|
2.水量 | 容器サイズ | 水量 |
500ml未満 500ml以上 |
100ml以上/容器 200ml以上/容器 |
|
3.残留塩素濃度 | 1~3ppm |
なお、リンサの洗浄効果は定期的に標準汚れボトルを用いて確認する必要がある。なお微生物が増殖しやすい果汁入り、ミルク入り炭酸飲料等については容器由来の微生物をより減少させる目的で2段リンサ(1段目の塩素濃度20ppm前後、2段目の塩素濃度1~3ppm)の採用事例も増えている。
(8) 充填
代表的なPETボトルへの充填について説明する。図4.PETボトル製造工程の例を示す。
プロポーショニングおよびカーボネーションを完了した製品液は、充填機(フィラー)でボトル詰めされ、密栓して製品となる。充填機は、炭酸飲料製造設備の中でも、最も高価な機械の1つであり、精密な構造を有し、緻密な運転管理を要する。しかも、製品品質や全体作業効率に対する影響も大きく、生産ラインの中心的な位置を占める。それだけに、運転や保守に十分な注意を払うべきである。
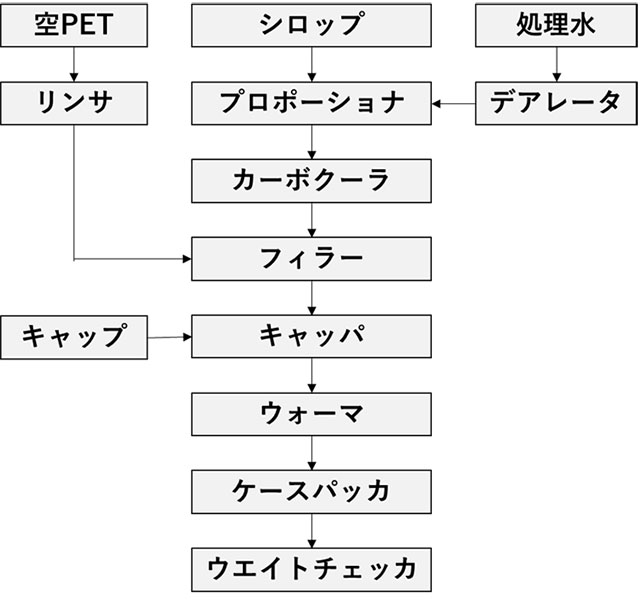
充填機にも、多くの型式、種類があり、細部の機構や作動は異なるものの、プレミックス方式においては、0.098~0.392MPa程度の加圧下で終点する加圧式充填方法が採られている。
充填機構は、次のようになっている。
- 充填機にボトルがセットされると、チャージングバルブが開いて、ボトル内は、充填機の製品液タンク(フィラーボウル)内の気体で充満され、フィラーボウル内の圧力と等しくなる。この圧力をカウンタプレッシャという。
- 製品液バルブが開いて、液がボトル内に入り、ボトル内の気体は充填バルブを通してフィラーボウルに移動する。フィラーボウル内の液面が下がると、カーボネータから液が流入して、ボウル内の液面を一定水準に保持する。
- ボトル内の製品液が、ベントチューブの孔まで達すると、ボトル内の気体の出口がなくなり、製品液の流入が自動的に停止する。
- ボトル内の製品液が詰まると、製品液バルブが閉じ、次にボトル内のヘッドスペースの加圧ガスを徐々に抜き、大気圧と平衡させる。
- ボトルを充填機から静かに離して、キャッパに転送する。
以上の工程は、1組の充填バルブで行われる。
充填の運転および保守について留意すべき事項を次にまとめる。
①起泡(フォーミング)
フォーミングは液が著しく泡立つことを意味し、これがPETボトルやびんなど容器への充填中に起これば、炭酸ガスの損失が増加し、場合によっては充填不足となる。PETボトルなど容器が充填機を離れるときに起これば内溶液が吹きこぼれて、量目不足となるばかりか、製造ラインに液がこぼれて微生物汚染の原因になる可能性がある。
フォーミングは、過飽和状態に溶解している炭酸ガスが、何らかの刺激によって、急に液から放出されて気泡となる現象であり、その原因としては、種々考えられるが、取り分け以下のような場合が多い。
- 液温またはPETボトル、びんなどの温度が高すぎる
- 製品液中にかなりの空気が存在する。例えばシロップや原料水中の空気が十分に脱気されていない。
- 充填前の液中に炭酸ガスが気泡として存在している
- 充填バルブの作動不良である
- PETボトルやびんの内面に傷、汚れがある
- 充填後、打栓機やキャッパへ移行する途中で容器が振動する
PETボトル充填の場合は、充填時のカウンタプレッシャにより、PETボトルが加圧膨脹し、充填後大気圧まで戻すときに収縮するため、高速での製造ラインや高ガスボリューム製品を製造する場合は起泡(フォーミング)に注意を払う必要がある。PETボトル詰め製品の製造において、完全にフォーミングを無くすことができないので、キャッパの前に処理水でのボトル口洗浄の工程がある。
➁充填バルブの保守
ロータリ式充填機においては、充填バルブは、1本1本が独立して機能を果たすものであり、仮に1本の充填バルブの作動が不良であれば、充填機が1回転するごとに、1本ずつの不良品を生産することにもなりかねない。したがって定期的な点検や部品交換などの保守管理が大切である。充填バルブは構造が複雑で、十分な洗浄・殺菌を行う必要があり、定期的に分解して、熱水、塩素水、等により殺菌され、衛生面での管理を徹底している。熱水を使用する場合には、ゴムや樹脂部品は損傷しやすいので留意する必要がある。
③充填機の保守
充填機は、製品液が直接空気に接触するので製品の品質への影響を配慮し、機械内、外部の汚染は必ず防止しなければならない。特に充填バルブの外部、フィラーボウルの周辺、安全カバー、スニフトカムカバー、ボトル・びんガイドなどが微生物汚染されやすいので、十分な洗浄と殺菌を行う。
④充填機への供給空気
フィラーボウルの液面制御、およびキャッパ巻締め末端などで用いる空気は、直接製品に触れる恐れがあるので、衛生的なクリーンなものでなければならない。一般的には、オイルレス圧縮機を使用し、数段階の除菌濾過(フィルタ)を通した空気を使用する。
➄巻締め(プラスチッククロージャ)
現在も主流はPETボトル飲料製品であることから、代表例として解説する。PETボトル飲料の口栓はプラスチック製のキャップが使用されている。プラスチックの材質としては主にポリプロピレン材やポリエチレン材がキャップとして採用されてい。また、キャップはライナ材あるいは中栓を有する2種類の材質から構成される2ピースタイプのものと、1種類の材質だけでできている1ピースタイプのキャップがある。各キャップは、成型性、密封性、いたずら防止機能などを持たせるための工夫がされている。
飲料用に使用されているプラスチックキャップは、キャップ内側にねじが形成されているスクリュキャップである。キャップはスクリュ式のキャッパで指定の巻締め角度まで締付けられる。キャッパのヘッドタイプはマグネットを組込んだメカニカルタイプとサーボモータを利用したサーボタイプがある。両タイプとも同様な巻締めが可能である。
キャップの密封性(シール)機構としては、アウトサイド&トップシール方式のキャップとインサイド&トップシールする方式のキャップがある。両シール機構のキャップともに既定の巻締め角度になると、ボトルキャップシール部に面圧が発生し内容液を密封する機構になっている。
巻締め成形された製品が正しく巻締められ、清浄な開栓性能、密封性能が得られているか確認のため、次の項目で検品管理されている。
➢ 巻締め角度の測定
規程の巻締め角度まで締められているか確認する。
➢ 開栓トルク値の測定
規定値内の開栓トルク値になっているか確認する。
➢ LB角度の測定
製品を開栓して密封性がなくなる(リーク)までの開栓角度(L角度)とブリッジ切れまでの開栓角度(B角度)を測定し、正常に巻締められているか、また、使用包材に問題がないか確認をする。
➢ 巻締め外観の確認
斜めかぶり、キャップの変形、ブリッジ切れ等の異常がないか確認するとともに管理を徹底する。
(9) 品質管理(工程検査)
炭酸製品の製造では、より良い製品をつくる上において工程品質管理は、非常に重要な検査である。近年、工程管理には工程モニタリング装置の導入が進み、自動化が図られている。
① 水の水質
炭酸飲料の製造に使用する水の水質は飲用適でなければならない。少なくとも1年に1回は、第3者機関で水質検査し、飲用適であることを確認する必要がある。製造開始前に、水処理(凝集沈殿処理、イオン交換処理、RO処理等)後の水質を検査し規格内であることを確認後使用する。表2.に各処理後の一般的な検査項目と頻度について示す。
No. | 管理項目 | RO処理/イオン交換処理 | 凝集沈殿処理 | ||
---|---|---|---|---|---|
規格 | 頻度 | 規格 | 頻度 | ||
1 | 外観 | 無色透明、濁り沈殿がないこと | スタート製造開始直前、4時間毎 | 無色透明、濁り沈殿がないこと | スタート、4時間毎 |
2 | 味・臭い | 異味・異臭がないこと | スタート、4時間毎 | 異味・異臭がないこと | スタート、4時間毎 |
3 | pH | 8.6以下 | スタート、4時間毎 | – | |
4 | 導電率 | 50μs/cm以下 | スタート、4時間毎 | – | – |
5 | 残留塩素 | 検出されないこと | スタート、4時間毎 | 検出されないこと | スタート、4時間毎 |
6 | Mアルカリ | – | 50ppm以下 (CaCO3として) |
スタート、4時間毎 | |
7 | 鉄分 | – | 0.01ppm以下 | 1日毎 | |
8 | 塩化物 | – | 300ppm以下 (NaClとして) |
1日毎 | |
9 | 蒸発残留物 | – | 500ppm以下 | 1日毎 | |
10 | 微生物 | 一般細菌、大腸菌群、カビ、酵母 | 毎週 | 一般細菌、大腸菌群、カビ、酵母 | 毎週 |
➁ガスボリューム
ガスボリュームの測定を精度よく行うためには、次の点に留意して行う必要がある。
- 測定前に、製品を恒温槽にて20℃程度(18~22℃)まで温め、液温を均一にする
- ガスボリューム測定器にかけ、スニフト(スニフトバルブを開放し、大気圧までゲージを戻す)を行う。スニフト操作を行うことによりヘッドスペース中の空気を除く
- 次に激しく振動させゲージ圧が一定値を示したら、その値を読み、製品の温度を測定し、スニフト用ガスボリュームチャートよりガスボリュームを求める。
補足:「スニフト」とは、ヘッドスペースのガスを放出する操作で酸素や窒素の影響を排除する目的で行う。スニフトは炭酸ガスも一緒に放出するので、行わない場合もある。炭酸ガス放出量が多くなりすぎないように、5℃以下で測定するのが原則。ガラスびん製品の場合は測定中にびんが破裂する可能性があるので防止の対策を行い測定する必要がある。
③糖度(Brix)
糖度の測定にはハイドロメータ(比重計)またはデンシティーメータ(密度計)を用いる方法が一般的である。測定に際しては、製品を20℃程度まで温めて行う。20℃を大きくはずれた温度で行う場合は、製品中の糖組成により温度補正値が異なるので注意を要する。また、炭酸ガスの残存は糖度に影響するので、測定は脱気後に行う。炭酸ガスの脱気は、超音波、撹拌機等により行う。バキューム方式による脱気は液の濃縮を起こさないように注意して行う必要がある。
(10) 品質管理(サニテーション)
すべての食品工場は、消費者に安全かつ衛生的に安心できる製品を提供する大きな責任があり、炭酸飲料製造工場にとっても例外でない。そのためには、原材料、容器のように直接製品の品質に直結するものは当然のこと、製造工場、製造ラインの各種機器類においても、その衛生状態を良好に保持していなければならない。いわゆる無果汁炭酸飲料の製造においては、一般に冷間充填(コールドフィリング)がおこなわれており、微生物の防除を主眼した衛生管理が厳しく行われる必要がある。
① 炭酸飲料製造工場における微生物
炭酸飲料は、炭酸ガス、酸味料を含有しているので、酸性を呈し、pHも低い。このような低pHで、比較的酸素の少ない条件下でも生育し、製品の外観や香味に影響を及ぼす可能性のある微生物として酵母があげられる。また、稀であるがカビの汚染も報告されている。大腸菌群をはじめ、病原菌や一般細菌については、酸性条件下では、たとえ混入したとしても、炭酸飲料製造工場においる衛生管理としては、まず酵母に重点が置かれている。
➁ 衛生管理
微生物による汚染を防止する方策としては、基本的に次の3つがあげられる。
➢ 外部からの汚染防止
工場内部がどんなに衛生状態がよく維持されていても、外部から侵入する微生物によって汚染される可能性はないとは言えない。それゆえ日常の製造において、工場外部から持ち込まれる微生物を最小限にする努力が必要である。
a) 原材料、包装材に付着して工場に持ち込まれる微生物や有害動物を防止するためなら、受入検査を厳密に行い、併せて供給工場の衛生状態の確認を行うなど、供給会社の協力も得る。
b) 工場外部から空気中に存在するかもしれない微生物を防除するために、例えばシロップ室や充填室を、清浄な空気により陽圧化しておく。
c) 従業員や外来者によって、工場内に持ち込まれる微生物を防除するため、製造ラインと通路は完全に分離する。
➢ 工場内における微生物の増殖防止
工場外部からの微生物の侵入を最小限に抑えることができても、全くゼロにすることはできない。微生物の増殖を防止する手段として、次の点について注意する。
a) 微生物の栄養源である砂糖などとの接触の機会をできる限り少なくする。また床面などにこぼれた糖液や工程中のタンクや配管中に残った糖液は速やかに洗浄する。
b) 微生物の増殖に必要な水分を排除し、工場内は、できる限り乾燥状態を維持する。
➢ サニテーション
上述の対策を実施しても、なお工場内に存在し増殖する恐れのある微生物を管理するために、工場や工程の状態に応じて、最もふさわしい方法により、定期的なサニテーションを実施する。
ⅰ) サニテ―ションの順序
サニテーションは、目で見ることのできるゴミやホコリを取り除く洗浄と、目に見えないが、製品に影響を与えるかもしれない微生物を、熱や薬剤などを用いて行う殺菌の2つの意味を持っている。したがってサニテーションを実施するに際しては、まず、洗剤を用いて、機械装置を十分洗浄し、糖分その他の原材料の残留をなくすことが大切である。これを行うには、用途に応じた適切な道具が使用される。道具としては、各種ブラシやスクィージ、またCIP洗浄装置、高圧洗浄装置、床磨機なども用いられる。布やモップなどは、ゴミが付着し微生物の発生源となる恐れがあるので注意が必要である。次いで、上記、熱水、塩素水などを用いて殺菌・除菌を行う。
ⅱ 定期的サニテーション
工場のサニテーションは、微生物の汚染を防止するための予防的な措置であるので、あらかじめ計画を立てて、組織的、定期的に行うことが効果的である。そのため、サニテーションの実施を、毎日、1週間毎、1月毎、1年毎に実施すべきことを定め、十分な時間が避けるように事前に準備をしておくことが重要である。
ⅲ) 殺菌方法
炭酸飲料製造工場で行われている主な殺菌方法は、熱水と塩素水によるものである。
a) 熱水殺菌
熱水殺菌では、殺菌箇所全体を高温にさらすことができるので、塩素殺菌では不十分な微細な隙間まで殺菌することができる。しかし機械装置の部品によっては、高温下でひずみや伸びを生じることで、損傷を受けるものもあるので、熱水の使用に先立って十分検討した上で行う。一般に熱湯の場合は、85℃で5分間以上、蒸気の場合は、3分以上を目安とするが、殺菌を行う箇所の規模と状況によって決定する。
b) 塩素殺菌
塩素は、最も広く使用されている殺菌剤である。通常は、塩素ガス、 サラシ粉、次亜塩素酸ソーダなどから調製した塩素水が使用される。塩素は微生物のみでなく、他の有機物や金属類にも強力な酸化剤として作用するので、濃度の高い塩素水を金属面に長時間放置すると腐食や錆を生じさせることがある。また殺菌箇所が洗浄不足で、ゴミや糖分が残っていると、これを酸化分解するために塩素が消費されてしまい、微生物が殺菌されないトラブルにつながることがある。殺菌後は、水で十分にすすぎ、残留塩素のないことを確認する。塩素水の濃度と浸漬時間は、対象となる殺菌箇所、材質によって異なるが、一応の指標として、ステンレス製装置では50ppmの塩素水で30分間を目安と考えるとよい。
c) 殺虫剤
工場内の昆虫類は、いかなるものであっても、食品の汚染源となる恐れがある。扉や窓は、できる限り閉鎖しておくか、網戸などを設けて昆虫類およびネズミの侵入を防止する。万が一侵入した昆虫を駆除するには、残留性のない噴霧殺菌剤や発煙殺虫剤を用い、駆除後は、十分換気をし、洗浄することが必須となる。
(11) 品質管理(製品検査)
①官能検査
官能検査(味覚検査)は、製品保証の検査項目の中で最も重要な検査の1つである。官能検査を実施するにあたり、次の項目に留意する必要がある。
➢ 環境
官能検査を実施する場合は、臭いのなく、騒音の少ない管理された場所で、温度は20℃前後で、相対湿度は60%前後が望ましい。換気により室内の有香物質を排除し、室外から清浄な空気を供給する必要がある。
➢ 検査員(パネル)
官能検査において、パネルの適正(能力)が問題となる。パネルの一般適性として、健康であること、身体的だけでなく心理的にも疲労がないこと。パネルの能力は訓練により向上するので、定期的に訓練を行い、能力を高める必要がある。また、検査を行う前には、刺激物の飲食は控え、喫煙を避けることが重要である。
➁微生物検査
炭酸飲料は炭酸ガスを含み、またpHが低いため、比較的微生物増殖に対し安定である。したがって炭酸飲料は一般的に殺菌工程がないため、製造ライン中で微生物の汚染源をなくすことが非常に重要になる。製造ラインを清浄に保つためには、毎日のサニテーションおよび週間ごとのサニテーションの実施が必須であり、充填時の微生物汚染を防ぐために、充填室の陽圧管理(空気動線管理)を徹底し、充填室への微生物の侵入を防ぐ必要がある。
➢ 落下菌検査(環境菌検査)
定期的な落下菌検査を工場の数ヶ所で実施し、落下菌の季節変動を調査・把握する。さらに常に落下菌を一定水準以下に管理するなど徹底し、充填室内を清浄に保つようにする。一般的な炭酸飲料製造工場の落下菌のガイドラインは次の通りになる。
充填室、シロップ室等(30分間 開放)
- 一般細菌:10CFU/プレート(90mm径)以下
- イースト:5CFU/プレート(90mm径)以下
- カビ:5CFU/プレート(90mm径)以下
- 大腸菌:0CFU/プレート(90mm径)
なお検査は床上500~1000mmの高さで、水やベバレージの飛沫の影響を受けない場所で実施する。
➢ 製品検査
炭酸飲料は炭酸ガスを含み、pHも低いため、一般に細菌は増殖せず、酵母およびカビの増殖が問題となる。したがって製品検査においては、酵母およびカビの検査を主に行う。
以上
【参考文献・引用】
- 「初心者のための食品製造学」著者:中島一郎 発行:(株)光琳
- 一般財団法人日本清涼飲料検査協会HP:http://www.seiryouken.jp/
- 一般社団法人全国清涼飲料連合会HP:http://j-sda.or.jp/