2019/11/21
【ゾーニング】&【動線】
Zoning & traffic line
~食品工場は次の考え方を取り入れ汚染を防止し、食品の安全・安心を実現する~
食品工場内を機能、用途などにより小部分に区域分けするが、「製造衛生環境別区分け」による事例で解説する。
- 一般区域(外部)と作業区域(工場内)を明確に分ける。
- 作業区域は、清浄度により清潔作業区域、準清潔作業区域、汚染作業区域の3つに分け、区域別にフロアの色を変える。(図⒈参照)
【ワンポイント!】
汚染作業区域とは、外部と接する可能性のある場所や、原材料や包材などの外部から持ち込まれた物品がある場所のこと。 - 清浄度の高い区域の室内の空気の圧力を上げ(陽圧)、人の出入りなどによる汚染空気の流入を避ける。
- 汚染区域から清潔区域への入室にはサニタリーエリアを通過しないと入室できない動線にする。
- ダンボール梱包された原材料・包材は製造エリア(清潔区域)に持ち込まない。
- 人・物・製品の動線を明確に分ける。(図⒈参照)
【ワンポイント!】
機械工場と食品工場が同じ敷地内にあるような場合、それぞれの従業員の動線の分離、既存建築物の有効活用、そして工場周辺住民への配慮から、近隣との共生も図る必要があり、食品工場を新設するときはゾーニングには重要なポイントになる。
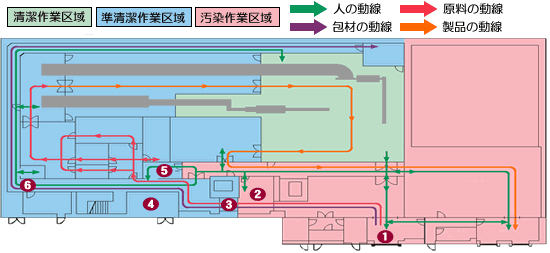
① 原料受入室
搬入時には、原料受入室と一時保管室の間のドアをインターロックし、外部からの汚染空気の流入を防止できる。(出荷時も同様に行う)
② 開梱室
入荷した原料、包材は開梱室でダンボール箱から工場内専用のプラスチックトレーに移すことにより、ダンボール箱などからの汚染を防止できる。
③ パスルーム
汚染作業区域と準清潔作業区域の間にパスルームを設置。開梱した原料・包材も全てに掃除機をかけ、付着しているほこりなどを除去できる。
④ 近隣住民への配慮
コンプレッサー、排気ダクト、エアコンの室外機など、音、臭気、熱を発する設備は全て敷地中央側に排出できるように設置する。(右図の赤い部分)
⑤ サニタリーエリア
汚染作業区域から清潔作業区域に戻る際には必ず、サニタリーエリアを通過し汚染を防止できる。
⑥ 従業員通路
製造エリアを横切ることなく目的のエリアに移動できるよう、外周に従業員通路を設置。
原料や包材が製造エリアを横切ることなく原料倉庫や包材ストック室へ運搬できる。
製造エリアへの出入りを最小限に抑えることができる。
人、物、製品の動線が明確に区別され、人、物、製品の交差による汚染を防止できる。
特に製造衛生環境別によるゾーニングは機能・用途別ゾーニングと重なるため、清浄区域の配置の適正化などの重要な検討事項となる。
生産施設内部の機能・用途別区域分けは、原材料保管ゾーン、原材料処理ゾーン、加工ゾーン、出荷ゾーンに分けられる。
工場内の人、物、製品の動きの量、方向、つながりを線により示すし、食品工場内の製造施設、機器・設備の配置などを計画する。
これらの流れを予測し、軌跡・通行量などを予め分析し、食品衛生的に矛盾なく流れる計画が動線計画である。
食品工場における製品のプロセスの流れは一方方向(one-way)を原則とし、製造途中の原材料相互ならびに原材料と完成品との動線交差が発生しないようにすることは工場計画のスタートとなる事項なので考慮が必要である。
以上